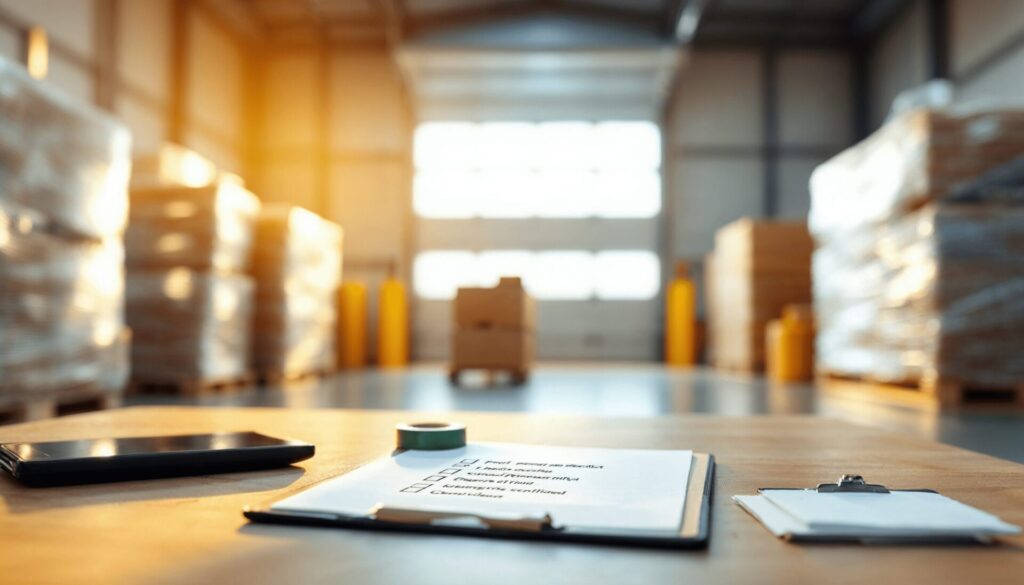
LTL Freight Shipping Checklist
Less Than Truckload (LTL) freight shipping has changed the way businesses move goods that don’t quite fill a standard 48- or 53-foot trailer. By sharing space with other shippers, you cut costs, reduce waste, and often meet tighter shipping deadlines. However, LTL shipping also involves intricacies that differ from Full Truckload (FTL) methods—think more frequent handling, complex route planning, and multiple potential touchpoints for errors.
A well-structured checklist is your best defense against these potential pitfalls. By systematically addressing each aspect—weight verification, labeling, packaging, and more—you position your shipment for a smooth transit. Below, you’ll find a detailed, step-by-step guide that you can follow or adapt to your own logistics workflow, ensuring every LTL shipment goes out on time, on budget, and with minimal surprises.
Introduction to LTL Freight
What “Less Than Truckload” Really Means
The term “Less Than Truckload” reflects a simple concept: when you have enough freight to surpass parcel shipping thresholds (usually around 150 pounds) but not enough to fill a dedicated truck (often 20,000 pounds or more), your cargo fits into LTL territory. Essentially, your freight shares trailer space with shipments from other organizations heading in a similar direction.
- Shared Costs: Rather than paying for an entire truck, you pay only for the space (and weight) your goods occupy.
- More Frequent Shipments: You don’t need to wait until you have a full truckload; smaller, more regular shipments become feasible.
- Environmental Benefits: Consolidating multiple loads in one truck can reduce the overall number of vehicles on the road, lowering emissions.
Why an LTL Shipping Checklist Is Essential
The complexity of LTL shipping lies in its shared nature: your freight travels alongside multiple other shipments, possibly switching trailers at cross-dock facilities. This increases opportunities for mislabeling, damage, or overlooked services like liftgate delivery. A thorough checklist ensures you:
- Provide Accurate Information: Avoid reweigh fees or reclassification charges.
- Streamline Communication: Prevent confusion by clarifying each requirement.
- Reduce Damages and Claims: By standardizing packaging and labeling procedures.
- Save Time and Money: Fewer back-and-forth calls with carriers, fewer missed deadlines, and reduced risk of paying for overlooked services.
Determining Shipment Readiness
Confirming Product Volume and Weight
Before diving into the shipping process, verify that LTL truly fits your load:
- Check Order Quantities: Ensure your final numbers match what’s actually on-hand. It’s not uncommon for last-minute orders or changes to slip by unnoticed.
- Verify Weights: Calculate the weight of the product itself plus all packaging materials. If you’re shipping multiple pallets, weigh each separately or use a large industrial scale capable of handling them together.
Be as precise as possible—carriers typically bill by hundredweight (cwt), so a small rounding error may lead to higher charges if the carrier reweighs your shipment.
Identifying Special Handling Needs
Not all shipments are created equal. Some items need special attention due to fragility, high value, or hazardous material status:
- Fragile Items: Glassware, electronics, and other breakables may require padded packaging and extra labeling.
- Hazardous Materials: Follow all regulations, including proper labeling, secure packaging, and specific documentation such as Material Safety Data Sheets (MSDS).
- Temperature-Sensitive Freight: Verify the carrier offers temperature-controlled or “reefer” services if necessary.
- Oversized Goods: If your freight is oddly shaped, excessively tall, or wide, confirm the carrier can handle it without additional equipment or fees.
Spotting these needs at the outset helps you secure accurate quotes and ensures your carrier is prepared.
Planning Pickup and Delivery
Scheduling Carrier Availability
Carriers generally operate within specific pickup windows rather than fixed times. A typical pickup window might stretch over a few hours. This flexibility helps carriers adjust routes and accommodate last-minute changes. On your side:
- Book Ahead: Provide at least one or two days’ notice—longer if you’re shipping during peak seasons or if you have special equipment needs like liftgates.
- Prepare the Loading Area: Pallets should be staged near the dock, fully wrapped, and labeled before the driver arrives.
- Confirm Vehicle Type: If your shipment is large or unusually tall, ensure the carrier’s vehicle can accommodate it.
Communicating Dock Hours and Limited Access
- Standard vs. Restricted Hours: Some warehouses or factories have narrow operating hours, or they might close for lunch breaks. Carriers typically need to know these in advance to avoid waiting fees.
- Limited Access Points: Residential neighborhoods, construction sites, military bases, schools, or places without a typical loading dock often incur extra fees. Mention these constraints when booking to ensure you receive an accurate quote.
By sharing this info upfront, you minimize on-the-spot confusion, which can lead to missed pickups or costly delays.
Choosing the Right LTL Carrier
Evaluating Coverage and Service Levels
Not every carrier services every region. Some focus on certain corridors, while others handle nationwide or even cross-border shipments. Match your load to a carrier with the appropriate geographic coverage:
- Regional Carriers: Often offer faster, more specialized routes within a limited footprint.
- National Carriers: Provide broader coverage, though sometimes at higher rates.
Also decide what balance of speed vs. cost you need. If time is tight, you might pay extra for expedited or guaranteed LTL services.
Checking Carrier Reputation and Reviews
- On-Time Delivery Rate: Look for carriers that meet their stated timelines consistently.
- Damage Claims History: A high rate of claims might suggest rough handling or careless routing.
- Customer Service: Whether it’s 24/7 call centers, online chat, or dedicated account managers, choose a carrier that’s responsive and easy to reach.
You can find insights on carrier performance through logistics forums, online review platforms, or by asking peers in your industry.
Freight Class and NMFC Verification
Understanding Density-Based Classification
The U.S. freight classification system sets class numbers from 50 to 500:
- Class 50–70: Denser goods like bricks or metal fixtures, usually cheaper to ship.
- Class 100–150: Moderately dense items, such as typical consumer products (furniture, electronics).
- Class 200–500: Light, bulky, or fragile items that often require careful handling or special stowing.
Calculate your freight density:
Density (lbs/ft³) = (Weight of Freight in lbs) ÷ [(Length in inches × Width in inches × Height in inches) ÷ 1728]
The higher the density, the lower (and cheaper) the class.
Confirming the Correct NMFC Code
Each product falls under a specific NMFC code, which affects freight class:
- NMFC Directories: You can consult official guides or use carrier websites to cross-reference your product type.
- Accuracy Matters: Incorrectly assigning a code can lead to a mismatch in freight class, causing carriers to reclassify your shipment and charge more.
It’s best to invest time upfront to verify you’re using the right code. If you ship the same item repeatedly, double-check the class only if the product or packaging changes.
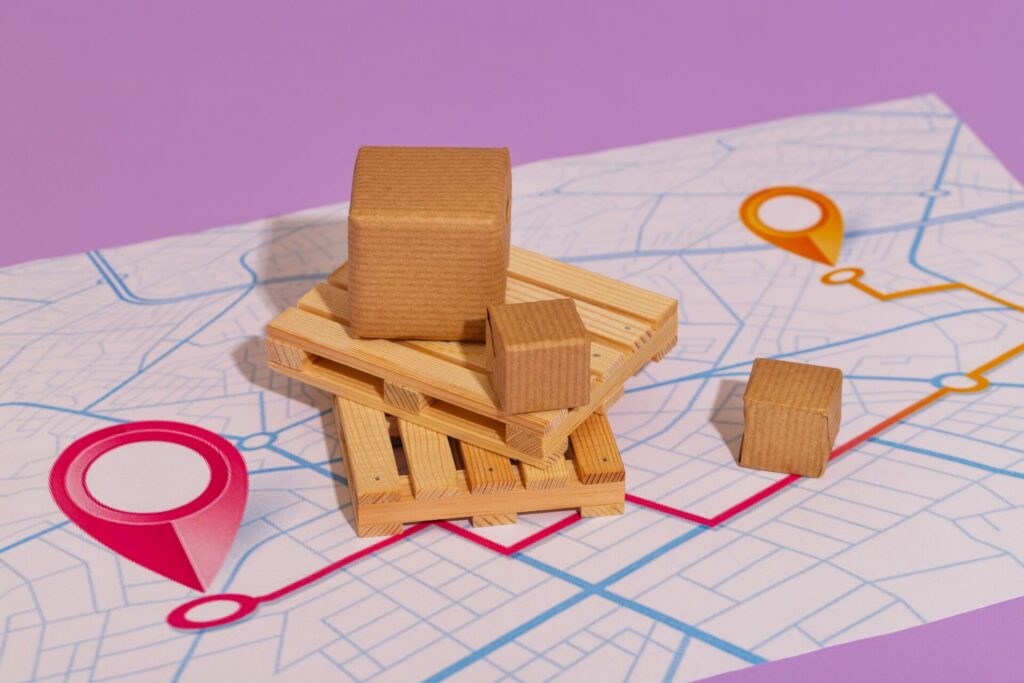
Accurate Weight and Dimensions
Weighing and Measuring Your Pallets
Aim for total precision. A few extra pounds can push your shipment into a higher weight bracket, raising your costs:
- Use a Calibrated Scale: Industrial-grade if possible.
- Double-Check Pallet Weight: Each wood pallet can weigh 30–70 pounds, depending on its type.
- Measure Dimensions After Palletizing: Because wrapping can add an inch or two in height or width if your load bulges.
Avoiding Reweigh Fees and Discrepancies
Carriers may reweigh if the declared weight seems off. If they discover your shipment is heavier, you could face:
- Reweigh Fee: Typically a flat fee or a percentage increase.
- Reclassification: If the new weight or dimensions push you into a higher freight class.
- Delayed Delivery: If the discrepancy causes confusion or re-routing at cross-dock terminals.
Posting photos of the shipment with visible scale readouts can help you dispute any inaccurate reweigh claims, though that’s rare if you’re certain of your numbers.
Proper Packaging and Palletizing
Selecting Quality Pallets and Crates
Not all pallets are created equal. Inspect them closely for:
- Splintering or Missing Boards: Compromised pallets can collapse.
- Mold or Rot: Especially if they were stored outside in damp conditions.
- Weight Capacity Ratings: Some light-duty pallets can’t safely handle the loads you might place on them.
If you’re dealing with international shipments, you may need heat-treated or fumigated pallets to comply with import/export regulations.
Securing and Wrapping Your Freight
- Stretch Wrap: Wrap in a consistent direction, applying multiple layers around the pallet base and up the sides. This keeps your goods stable, preventing them from shifting en route.
- Straps or Bands: If your shipment is especially heavy or tall, strapping can reinforce it, keeping boxes from toppling.
- Corner Protectors and Edge Boards: Add to the corners of boxes for extra defense against external knocks.
- Stacking: Place heavier items on the bottom and lighter, more fragile items on top. Ensure nothing overhangs the pallet edge.
Careful attention to packaging can substantially lower the chance of damage claims or refused deliveries.
Labeling and Documentation
Marking Fragile or Hazardous Goods
- Fragile Labels: Use bold, high-visibility stickers if your items can break easily. Carriers won’t guarantee the same level of white-glove care, but visible labeling raises awareness.
- Hazmat Compliance: Follow DOT (Department of Transportation) regulations. This includes proper hazmat labels, placards, and documentation like the MSDS and emergency contact details.
Failing to label hazardous or fragile items accurately can lead to fines or liability issues if your shipment causes damage or harm.
Ensuring Pallets Have Clear Shipping Labels
Each pallet should display:
- Shipper and Consignee Info: Full addresses, contact numbers, purchase order references, or other relevant IDs.
- Carrier-Proof Labeling: Use waterproof, tear-resistant labels, ideally on two or more sides of the pallet.
- Orientation Indicators: For items that must remain upright, “This Side Up” or arrow labels are invaluable.
Don’t rely solely on the Bill of Lading (BOL). If your BOL and the physical labels on your shipment clash, the carrier may prioritize the BOL data, leading to routing mix-ups.
Preparing the Bill of Lading (BOL)
(H3) Key Elements of a BOL
A BOL is a legal contract between you (the shipper) and the carrier. It typically includes:
- Shipping and Receiving Addresses: With correct zip/postal codes, building numbers, and any suite or unit info.
- Date of Shipment: Helps track transit timelines and potential delays.
- Item Description: This includes the freight class, NMFC code, weight, number of pallets, and any special instructions.
- Payment Responsibility: Clearly state who pays the freight charges: the shipper, consignee, or a third-party logistics provider (3PL).
Always supply multiple copies of the BOL: one for your records, one for the carrier driver, and one for the receiving party.
Verifying Contact and Payment Details
Even minor typos (like a wrong phone number or misspelled street name) can cause big issues. Confirm that all contact information is correct, especially if your shipment goes to a large facility. Also clarify payment terms:
- Prepaid: Shipper pays.
- Collect: Receiver pays.
- Third-Party Billing: A 3PL or another entity handles the costs.
If your arrangement is collect or third-party billing, ensure that party is aware of the shipment—no one likes surprise invoices.
Accessorial Services Checklist
Liftgate, Inside Delivery, and Beyond
Accessorials are extra services not included in the base LTL rate. Some common examples:
- Liftgate: Required if you don’t have a dock or forklift.
- Inside Delivery: The driver carries your freight beyond the loading dock or building entrance.
- Residential Delivery: Shipping to a home or small business in a residential area typically triggers an extra fee.
- Limited Access Delivery: Construction sites, farms, schools, or military bases often fall into this category.
Failing to mention any of these needs upfront can result in last-minute fees and possibly a rescheduled delivery.
Scheduling Appointments and Limited Access
If your dock is only open between, say, 9 a.m. and 2 p.m., or if you need the carrier to call ahead before attempting delivery, this may require an appointment scheduling fee. Provide all constraints when you book. This transparency ensures the carrier shows up prepared and you only pay for services you truly need.
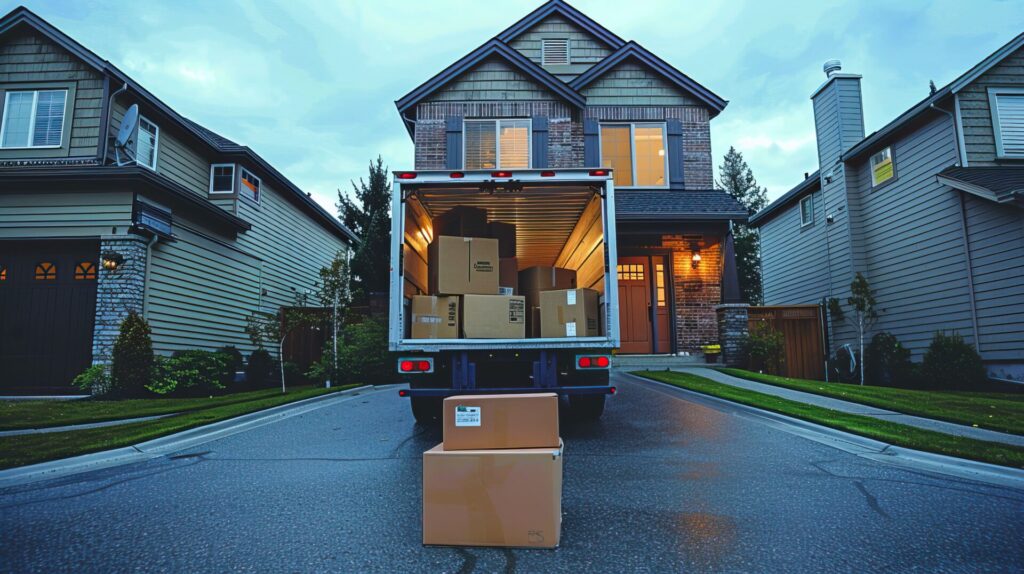
Insurance and Liability Coverage
Determining Adequate Carrier Liability
Carriers typically offer limited liability, often based on weight, not the actual value of your goods. For instance, a carrier might cap coverage at a few dollars per pound. If your product is high-value (e.g., electronics, specialized machinery), you risk significant financial loss if something goes wrong.
Exploring Third-Party Insurance Options
- Supplemental Policies: Purchase extra coverage for high-value items.
- Cargo Insurance: You can often buy cargo insurance through a 3PL, freight broker, or an independent insurer.
- Cost-Benefit Analysis: Weigh the premium against potential replacement costs. If your items are easily broken or extremely pricey, extra insurance might be worth every penny.
Rate Quotes and Cost Management
Comparing Multiple Carriers and Brokers
You don’t have to stick to a single carrier:
- Spot Quotes: For a one-time or occasional shipment, request quotes from multiple carriers.
- Contract Rates: If you ship regularly, look into contracting with a single carrier or a 3PL for consistent, potentially discounted pricing.
Freight brokers can also help you find the best deal, but always confirm they’re reputable and transparent with fees.
Watching Out for Hidden Fees
In LTL shipping, base rates can appear low until you factor in:
- Fuel Surcharges: Typically pegged to national fuel index rates.
- Reweigh or Reclassification Fees: If your declared weight or class doesn’t match.
- Detention: If the driver waits too long at pickup or delivery.
- Redelivery or Reconsignment: If the wrong address is specified or if no one is present to receive the shipment.
A thorough read of your carrier’s tariff (their rulebook) helps you anticipate and plan for these extra charges.
Tracking and Real-Time Updates
Using Technology Tools or Carrier Portals
Many carriers now offer digital solutions to keep you updated:
- Online Dashboards: Log in to see your shipment’s location, estimated delivery time, and any route deviations.
- Mobile Apps: Quick push notifications or text alerts can warn you about delays, so you can notify the receiving party in real time.
If you’re dealing with a broker or 3PL, they may have their own platform aggregating data from multiple carriers, giving you a one-stop shop for tracking.
Communicating Delays and ETA Changes
Despite planning, unforeseen factors like weather or mechanical issues can delay shipments. Stay proactive:
- Carrier Contact: Confirm you have direct contact details for dispatch.
- Customer Notification: If you’re shipping to a client, let them know about revised ETAs the moment you learn them.
- Contingency Planning: For time-sensitive goods, consider expedited options or partial shipments if the original LTL route faces disruptions.
Delivery Verification and Claims
Inspecting Cargo Upon Arrival
Before signing for the delivery, take a moment to:
- Check Pallet Count: Ensure you’re receiving the correct number of pallets or boxes.
- Examine for Damage: Look for holes in the stretch wrap, crushed corners, or wet packaging.
- Note Discrepancies: If you see any issues, write them on the delivery receipt. You can’t typically claim damage once you’ve signed a “clean” bill of lading.
Filing Damage or Loss Claims Promptly
- Deadline Awareness: Some carriers require claims within 5–15 days. Missing this window weakens your case.
- Documentation: Photos, the BOL copy with notes on visible damage, and any relevant invoices or receipts.
- Carrier Procedures: Follow the carrier’s specific claim steps, which often include an online or paper form.
- Settlement: If your item was underinsured, you might only receive minimal coverage based on weight, not actual value.
Act quickly. Delays in filing often result in a denied claim, leaving you stuck with replacement costs.
Conclusion
LTL freight shipping offers an agile, cost-effective way to move goods when you don’t have a full trailer’s worth of cargo. By paying close attention to packaging, labeling, and correct freight classification—and by staying upfront about accessorial needs—you can sidestep the most common pitfalls. A robust checklist serves as your roadmap, taking you step by step through each task and verification.
Whether you’re a small business venturing into new markets or an established company refining your logistics workflow, LTL shipping can be a strategic advantage when done correctly. Thorough preparation, clear communication with carriers, and a strong paper trail not only protect your freight from damage or misrouting but also defend against costly reclassification or reweigh fees. Embracing the guidelines in this checklist paves the way for on-time, on-budget deliveries—ensuring your goods get where they need to go, hassle-free.
How useful was this post?
Click on a star to rate it!
Average rating 0 / 5. Vote count: 0
No votes so far! Be the first to rate this post.