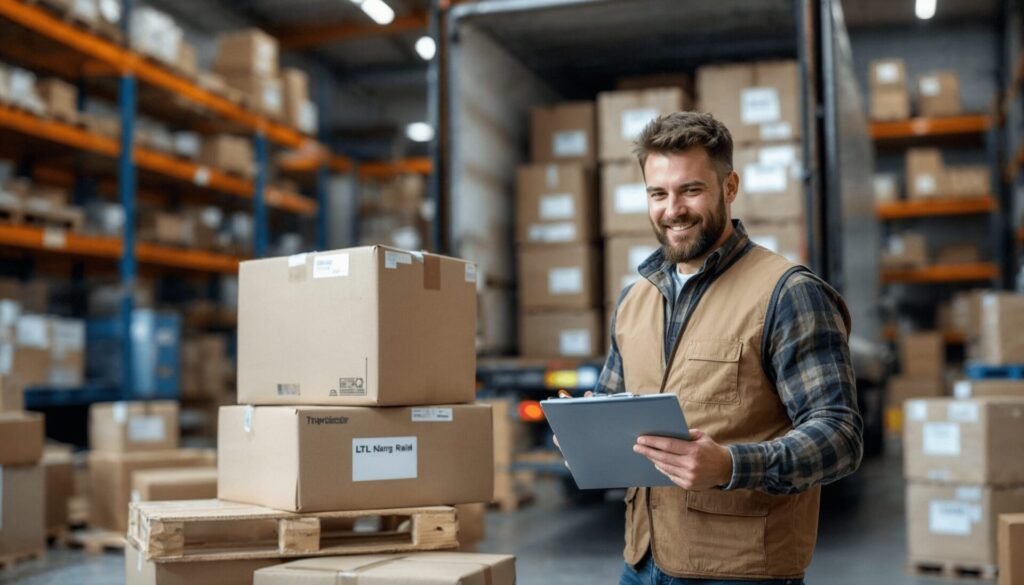
LTL Freight Guide for Small Businesses
For small businesses, shipping can be one of the trickiest parts of getting your product from the manufacturing floor or warehouse to your customers’ doorsteps. If your cargo is too big for parcel carriers but too small to fill an entire truck, you’re stuck in that awkward middle ground—unless, of course, you embrace Less Than Truckload (LTL) freight. In this comprehensive guide, we’ll walk through what LTL freight is, why it’s such a game-changer for smaller enterprises, and how to implement it seamlessly within your logistics strategy.
Think of LTL like a carpool for your products: you’re splitting the cost of fuel and driver time with other shippers headed in roughly the same direction. This means you can pay for just the space you need rather than footing the bill for a half-empty truck. Along the way, we’ll discuss everything from freight classes and cost considerations to best practices for packaging and scheduling. By the end, you’ll be able to decide if LTL makes sense for your business and, if so, how to take full advantage of it.
Introduction to LTL Freight
Definition of “Less Than Truckload”
Less Than Truckload (LTL) shipping is a method designed for shippers who need to transport freight that doesn’t fill an entire trailer. These shipments typically weigh between 150 and 15,000 pounds. Multiple businesses will share a truck, and the freight is consolidated at distribution centers or cross-docking terminals before heading to its final destination. You pay based on the portion of the trailer space your cargo occupies, making it a cost-effective solution for many small and medium-sized loads.
How LTL Differs from Other Shipping Methods
- Full Truckload (FTL): Great if you have enough freight to fill an entire truck. Otherwise, you end up paying for unused space.
- Parcel Services: Ideal for small, lightweight packages but can get expensive once you exceed certain weight or dimension thresholds.
- Partial Truckload or Volume LTL: Falls in between LTL and FTL, offering fewer handling points and often appealing rates for mid-sized shipments.
LTL stands out by serving businesses whose shipping demands shift between large parcel and near-full trailer loads. For many small businesses, it fills a critical gap in the shipping spectrum.
Why LTL Freight Matters for Small Businesses
Balancing Budget and Demand
Small business owners often juggle tight budgets and unpredictable order volumes. You may not always have enough product to fill an entire truck, yet you still need consistent and reliable shipping solutions. LTL allows you to send freight in smaller, more frequent batches, letting you maintain leaner inventory levels while meeting customer expectations. You pay for only the trailer space and weight you use, freeing up funds to invest in other parts of your business.
Managing Limited Storage Space
Without massive warehouse facilities, holding onto large quantities of unsold product can become problematic. By using LTL, you can schedule shipments more frequently and avoid overstocking. This approach is particularly advantageous if you sell seasonal or trend-dependent goods, where being stuck with stale inventory can quickly hurt your bottom line.
Understanding Freight Classes
The Basics of Freight Classification
The freight industry categorizes goods based on freight classes, which range from 50 to 500. Four primary factors determine the class:
- Density (pounds per cubic foot)
- Stowability (How easily can the freight be stowed or stacked?)
- Handling (Does the freight require special care or extra labor?)
- Liability (Value of the cargo and likelihood of damage or theft)
Lower classes often represent denser, less fragile items (e.g., bricks), while higher classes cover lighter, delicate, or bulky items (e.g., pillows). Each classification affects the shipping rate, so getting it wrong can either cost you in overcharges or lead to surprise invoices if a reclassification is done by the carrier.
Common Mistakes in Determining Freight Class
Many small businesses underestimate or overestimate the density of their products. Some assume if it’s fragile, it must have a high freight class—only to find out later that size and weight are the biggest determining factors. Additionally, not accounting for packaging dimensions leads to underreported shipment sizes, which can result in unexpected rate adjustments.
Key Advantages of LTL for Small Businesses
Cost Savings Through Consolidation
A principal draw of LTL is cost efficiency. By consolidating shipments from multiple shippers, carriers split fuel, labor, and other overhead expenses among all parties. In other words, you share the ride. It’s akin to chipping in for a group taxi rather than booking a luxury limousine for a single person. For small businesses operating on shoestring budgets, these savings can add up quickly.
Flexibility in Shipment Sizes
LTL accommodates fluctuating freight volumes. Whether you’re sending out 10 pallets one week or just 2 the next, carriers can match your load with others heading in a similar direction. This flexibility allows you to keep sales channels open without waiting to gather a full truck’s worth of goods.
Reduced Environmental Footprint
Consolidating multiple shipments into fewer trucks cuts down on the number of vehicles on the road, leading to lower emissions overall. For eco-conscious businesses, using LTL is a tangible way to reduce your carbon footprint. This environmental benefit can also be a selling point for customers who value green logistics.
Cost Considerations
Rate Factors: Weight, Dimensions, and Distance
Carriers typically base LTL rates on three key factors:
- Weight: Heavier shipments can sometimes qualify for lower per-pound rates, but going too heavy may push you into the realm of FTL.
- Dimensions: The physical space your freight occupies is crucial, especially if it’s bulky but relatively lightweight.
- Distance: Naturally, the farther your goods travel, the higher the rate. However, shipping across popular routes might be cheaper due to economies of scale and more carrier options.
To optimize costs, accurately measure and weigh your freight, and keep an eye out for route options that might lower expenses.
Extra Fees and Accessorial Charges
Beyond the base rate, carriers can tack on additional fees for specialized services:
- Liftgate Service: If your pickup or drop-off location lacks a loading dock.
- Inside Delivery: If the driver has to move freight beyond the loading bay or front door.
- Residential Delivery: Shipping to a home or non-commercial location can incur extra charges.
- Limited Access Fees: Extra charges for deliveries to places like schools, farms, or construction sites.
Understanding and budgeting for accessorial charges helps you avoid surprise bills that could knock your carefully planned costs out of balance.
Packaging and Palletizing 101
Best Practices for Palletizing
How you package and stack your freight can influence both cost and safety. Proper palletizing ensures your shipment remains stable, reduces damage, and can even improve how carriers quote your freight class. Key tips:
- Use Quality Pallets: Avoid broken or warped wood that can lead to collapsed loads.
- Secure with Shrink Wrap or Strapping: Prevent boxes from shifting en route.
- Distribute Weight Evenly: Placing heavy items on top of lighter ones is a recipe for crushed merchandise.
Protecting Fragile Goods
If you’re shipping easily damaged items like glassware, electronics, or artwork, add protective layers such as bubble wrap, foam inserts, or corner protectors. Label your pallets as “fragile” if needed. While every piece of cargo should be handled carefully, giving carriers clear instructions helps reduce the chance of mishandling.
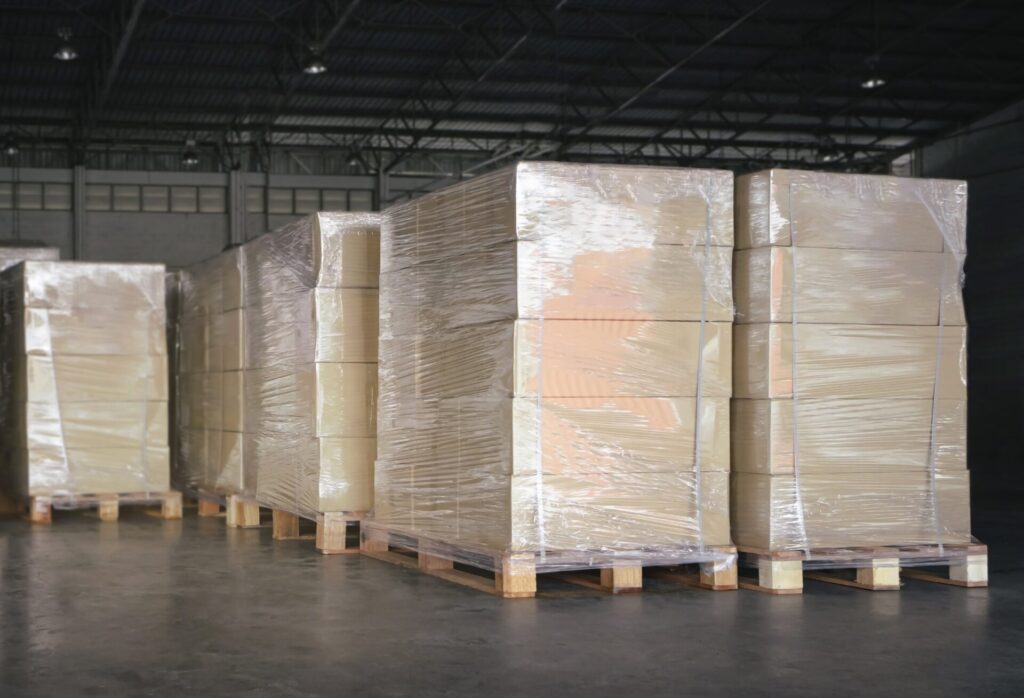
Choosing the Right LTL Carrier
Evaluating Carrier Reputation
Not all carriers operate with the same reliability or coverage range. Before locking in a contract, look into:
- On-Time Delivery Rate: How often do they meet their promised timelines?
- Damage Claims Record: Frequent damages might signal rough handling or inadequate staff training.
- Coverage Area: Ensure they service both your origin and destination.
- Customer Service: Are they easy to reach if issues arise?
Reading online reviews and talking to other small business owners can help you separate the reputable carriers from the rest.
Negotiating Contracts and Rates
Carriers may offer volume-based discounts or contract pricing if you can commit to shipping a certain number of pallets per month. If you’re shipping sporadically, don’t be afraid to shop around. Freight brokers or third-party logistics providers (3PLs) can also leverage their networks to secure better rates. Building a long-term relationship with a carrier can yield personalized attention and more favorable terms.
Scheduling and Pickup Procedures
The Importance of Accurate Paperwork
Your Bill of Lading (BOL) is the contract between you and the carrier. It outlines the type of goods, weight, dimensions, origin, and destination. Think of it like a plane ticket for your pallets—if the info is wrong or incomplete, your shipment could go to the wrong place or be reclassified, resulting in fee adjustments.
- Include Correct Freight Class: A mismatch between your declared class and the carrier’s inspection can cause cost disputes.
- Specify Any Special Services: If you need a liftgate, limited access, or inside delivery, ensure it’s clearly stated.
Coordinating Pickup Windows
Carriers typically provide a pickup window rather than a precise time. Communicate the pickup date and any time constraints well in advance. Having your shipment ready—palletized, labeled, and shrink-wrapped—helps speed up loading and avoids additional waiting fees. If possible, give yourself a buffer in case the carrier arrives earlier or later than expected.
Tracking and Documentation
Bill of Lading Essentials
Your Bill of Lading does more than just list what’s in your shipment; it also specifies terms, includes contact details, and confirms who is responsible for freight charges. Keep multiple copies—one for the driver, one for your records, and possibly one attached to the freight. If something goes awry, the BOL is your go-to reference.
Real-Time Updates and Shipment Visibility
Modern LTL carriers often offer online tracking portals or mobile apps, letting you see where your freight is in transit. For a small business, this visibility can be a big deal—you can confirm deliveries, spot potential delays, and update customers accordingly. Timely communication enhances your professional reputation and reduces guesswork in the shipping process.
Minimizing Damage and Loss
Proper Handling Instructions
Label each pallet clearly with any special instructions (“This End Up,” “Fragile,” etc.). While carriers handle freight of all shapes and sizes, your items might require extra care. By proactively informing the driver or terminal staff, you help them understand how to load your cargo safely.
Claims and Insurance Basics
Even with precautions, damage can still occur. Most carriers offer limited liability based on a dollar-per-pound rate, which might not cover high-value items. For expensive or delicate shipments, consider buying additional insurance. If damage happens:
- Document Everything: Take photos of the pallet’s condition before and after shipping.
- Note Damage on Delivery Receipt: Don’t sign off on a clean bill if you see obvious damage.
- File Claims Promptly: Carriers typically have strict deadlines for claims submission, so act fast.
Using Technology and Software Tools
Freight Management Systems (FMS)
Freight Management Systems (FMS) centralize the booking, tracking, and documentation process. You can compare carriers, print labels, and view rates side by side. This efficiency can be a lifesaver if you’re juggling multiple shipments each week.
Automated Quoting Platforms
Online marketplaces or load boards let you input shipment details (weight, dimensions, origin, destination) and instantly see multiple carrier quotes. Some platforms also show transit times, allowing you to strike a balance between cost and speed. Automated quotes take the guesswork out of budgeting for LTL, and they’re particularly handy for small businesses without a dedicated logistics department.
Common Mistakes to Avoid
Incorrect Freight Class or Weight
LTL carriers reweigh or reclassify freight if something seems off. Not only does this lead to unexpected surcharges, but it can also cause delays. Always measure accurately, include packaging in your dimensions, and verify your freight class. If you’re unsure, consult online freight class calculators or ask your carrier for guidance.
Last-Minute Shipping Surprises
If you haven’t planned ahead, you might find your ideal carrier doesn’t have availability when you need it. Booking shipments on short notice can also limit your negotiating power on rates. Try to schedule at least a day or two in advance—longer if you’re shipping during busy seasons like holidays or quarter-end.

Implementing LTL Best Practices
Combining Orders Strategically
One of the overlooked ways to maximize LTL is by combining orders shipping to the same region. If you know you have multiple small deliveries going to customers in, say, the same state or region, coordinate them so they can leave on a single shipment. This strategy can lower your overall freight rate because carriers often offer better pricing for higher aggregate weight or multiple pallets.
Communicating with Carriers Proactively
Good communication doesn’t just happen at pickup. Stay in touch with your carrier throughout the transit process. If you or your customer notices any potential issues—like construction blocking a delivery address—share that information ahead of time. Carriers appreciate heads-up alerts, and proactive communication can spare you from extra fees or late deliveries.
Conclusion
LTL freight offers a tailored solution for small businesses that need to move moderate loads without the cost burden of booking an entire truck. By consolidating shipments, businesses can scale their logistics processes more efficiently and improve cash flow. The trick lies in nailing down the details: from choosing the correct freight class and packaging your goods properly, to picking carriers that align with your reliability and budgetary needs.
Whether you’re shipping a handful of pallets per month or ramping up for a surge in demand, LTL freight can slot neatly into your workflow. Its flexibility, cost efficiency, and environmental advantages make it an attractive choice in a rapidly changing market. Remember that success depends on accurate measurements, proper documentation, and thorough communication at every stage. Embrace LTL shipping with a well-informed strategy, and you’ll be well on your way to creating a more nimble and cost-effective supply chain—one that helps your small business thrive.
How useful was this post?
Click on a star to rate it!
Average rating 0 / 5. Vote count: 0
No votes so far! Be the first to rate this post.