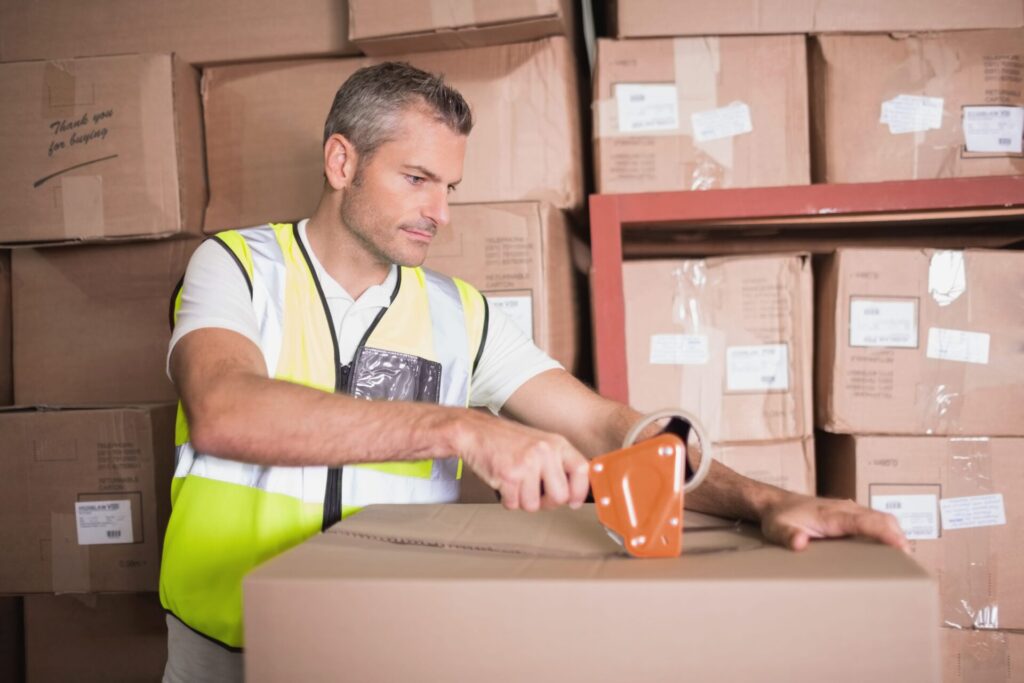
Best Practices for LTL Freight Packaging
Less Than Truckload (LTL) freight shipping offers a flexible, cost-effective way to move smaller loads without the overhead of a full truck. However, success hinges on one crucial element: how well you package your freight. LTL shipments often travel through multiple terminals and can be handled by several different carriers before reaching their destination. Poor packaging at any point in that chain can result in damage, delays, and extra fees.
This guide covers the most effective strategies for protecting your products in an LTL environment. From selecting the right pallets to layering fragile goods and incorporating eco-friendly packaging, we’ll show you how to ensure your cargo arrives in pristine condition—and how to do it without inflating shipping costs. By the end, you’ll have a blueprint for stress-free LTL shipments that delight customers and keep your budget in check.
Why LTL Packaging Matters
Multiple Handlings and Transfers
In contrast to Full Truckload (FTL) shipping, which often travels directly from point A to point B, LTL freight typically goes through multiple touchpoints. Your goods might get loaded and unloaded several times as they pass through carrier terminals and cross-dock facilities. Every transfer invites potential risks:
- Forklift Damage: Improper handling with pallets that aren’t secured can lead to broken items.
- Mix-Ups: If your items aren’t clearly labeled, they could end up in the wrong truck.
- Increased Vibration: As your freight moves from one vehicle to another, road and mechanical vibrations can loosen poorly secured items.
Cost Implications of Poor Packaging
When packaging isn’t up to par, you open the door to:
- Damage Claims: Carrier liability often has limits; if your goods are inadequately protected, you may be on the hook for replacements.
- Reweigh/Reclassification Fees: If loose or damaged packaging causes changes in your freight class or weight, carriers may charge extra.
- Delivery Delays: Damaged freight might need reworking, re-labeling, or special handling, extending your timelines.
Assessing Your Freight’s Needs
Weight, Dimensions, and Fragility
Before designing any packaging strategy, evaluate the basic characteristics of your shipment:
- Total Weight: Heavier loads need sturdier pallets and more stable wrapping techniques.
- Dimensions: The taller and wider your shipment, the higher the chance of tipping or load shift.
- Fragility: Items like glass, electronics, or ceramics demand extra cushioning and careful stacking.
If your product dimensions or weight significantly exceed standard pallet sizes, custom crating or special handling may be necessary.
Identifying Special Handling Requirements
Are your goods temperature-sensitive, hazardous, or extremely fragile? Make these needs known to the carrier well in advance. You might need special labeling, protective insulation, or even specific scheduling. Providing accurate details ensures carriers are prepared and helps avoid extra fees or last-minute confusion.
Choosing the Right Pallets
Wood vs. Plastic Pallets
- Wooden Pallets: Common, cost-effective, and robust enough for most LTL loads. However, they can have uneven surfaces or splinters that damage packaging if they’re of poor quality.
- Plastic Pallets: Durable, clean, and less likely to harbor pests or splinters. Typically cost more than wood but can be reused many times, potentially offsetting the initial investment.
For international shipments, ensure that wooden pallets meet ISPM 15 standards (heat-treated or fumigated) to comply with import/export regulations.
When to Use Custom Crates
If you’re shipping uniquely shaped or high-value items—like machinery parts or fragile artwork—custom crates may offer the best protection. While pricier than standard pallets, they can significantly reduce damage risk, saving you money in the long run.
Proper Stacking and Load Stabilization
Distribution of Weight
Even weight distribution is vital for preventing pallets from tipping or collapsing. Place heavier boxes at the bottom, lighter ones on top, and avoid creating tall, narrow stacks that are prone to toppling.
- No Overhang: Keep products within the pallet footprint; overhanging items risk damage from external impacts.
- Vertical Alignment: Align boxes for maximum surface contact, creating a stable “tower” effect.
Stretch Wrap and Strapping
- Stretch Wrap: Wrap your entire stack tightly, including the pallet base. Consider multiple layers and ensure the wrap reaches the bottom to keep boxes firmly in place.
- Straps or Bands: For heavier loads, plastic or metal strapping adds reinforcement. You can apply straps vertically or horizontally, depending on the configuration.
Cushioning and Internal Protection
Bubble Wrap, Foam, and Dunnage
For fragile or high-value items, internal protection matters just as much as external wrapping:
- Bubble Wrap: Ideal for surface protection.
- Foam Inserts: For items with delicate corners or edges.
- Dunnage: Fill empty spaces within boxes with paper, air pillows, or foam peanuts to prevent shifting.
Layering Fragile Goods
If you’re stacking multiple layers on a pallet:
- Use Corrugated Sheets: Place a sheet of cardboard or foam between layers.
- Stack Lighter or Fragile Boxes on Top: Reduce the weight pressed down on fragile items.
- Separate Fragile and Heavy Items: If your shipment has a mix of both, consider using multiple pallets.
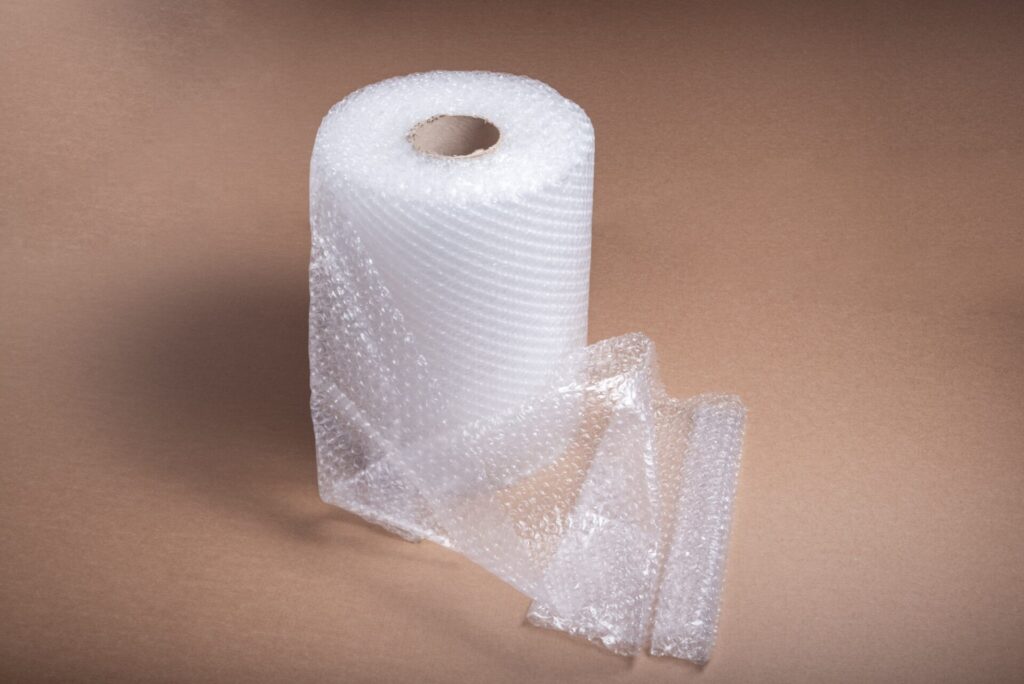
Labeling Your Freight
Standard Shipping Labels
At a minimum, ensure each pallet has a clear label indicating:
- Origin and Destination: Full addresses, including suite numbers if applicable.
- Shipper and Consignee Contact Details: Names, phone numbers, and possibly email addresses.
- Reference or PO Number: So carriers can link to the right shipment.
Fragile, Hazardous, or Perishable Markings
Beyond basic shipping labels, consider:
- Hazardous Material Placards: Follow DOT regulations if shipping hazardous substances.
- Fragile or “This Side Up” Labels: Helps handlers understand how to move your pallets.
- Temperature Requirements: For perishable goods, indicate if refrigeration or temperature control is needed.
Palletizing for Mixed Shipments
Sorting by Destination
Sometimes, multiple customers’ orders are combined on the same pallet or multiple pallets. To avoid confusion:
- Group by Consignee: Ensure each customer’s products are on a separate pallet or distinctly partitioned.
- Color-Coded Labels: Differentiate each segment with unique stickers or tags, especially if SKUs look similar.
Keeping SKUs Separated
If you must ship various products together, keep each SKU segregated:
- Partition Boxes: Cardboard dividers inside crates or boxes can help.
- Mark Boxes with Large, Visible SKU Codes: If handlers know exactly where each item is, they’re less likely to mix them up.
Maximizing Cube Utilization
Filling Voids and Minimizing Shifting
Open spaces within or between boxes can cause items to shift in transit. Minimizing these gaps:
- Add Filler Material: Paper, foam, or air pillows absorb shock and prevent movement.
- Use Dividers: Cardboard or foam partitions maintain each item’s position.
Reducing Dimensional Weight Penalties
Carriers often use dimensional weight for pricing. If your shipment is large yet lightweight, you could pay more. Pack items as compactly as possible:
- Break Down Components: If items can be shipped disassembled, you save on space.
- Avoid Excessive Box Size: Don’t stick a small item in a massive box that inflates your dimensions.
Using Edge and Corner Protectors
Preventing Compression Damage
Edge guards—usually cardboard or plastic—attach to pallet corners to distribute weight and absorb impacts. They’re especially useful if:
- You’re Stacking Multiple Pallets: They help protect lower layers from top-pallet compression.
- Your Freight Is Easily Crushed: This could include soft goods or cartons with delicate contents.
Reinforcing Pallet Corners and Edges
Angle boards or corner protectors also protect packaging edges from forklift tines or other sharp objects. While they add a small cost, they can drastically reduce damage rates and subsequent claims.
Sealing and Wrapping Techniques
Heat-Shrink vs. Stretch-Wrap
- Heat-Shrink Wrapping: Typically used for sealing entire pallets of uniform items. Provides a tight seal but can be time-consuming and requires specialized equipment.
- Stretch-Wrap: The go-to option for most LTL loads. Quick, easy, and versatile. Just ensure enough tension.
Strapping High-Value or Heavy Loads
If your load is especially heavy or pricey:
- Polyester Straps: Offer good tension and shock absorption.
- Metal Straps: Common for very heavy loads or industrial equipment. Can dig into boxes if not used with protective corners.
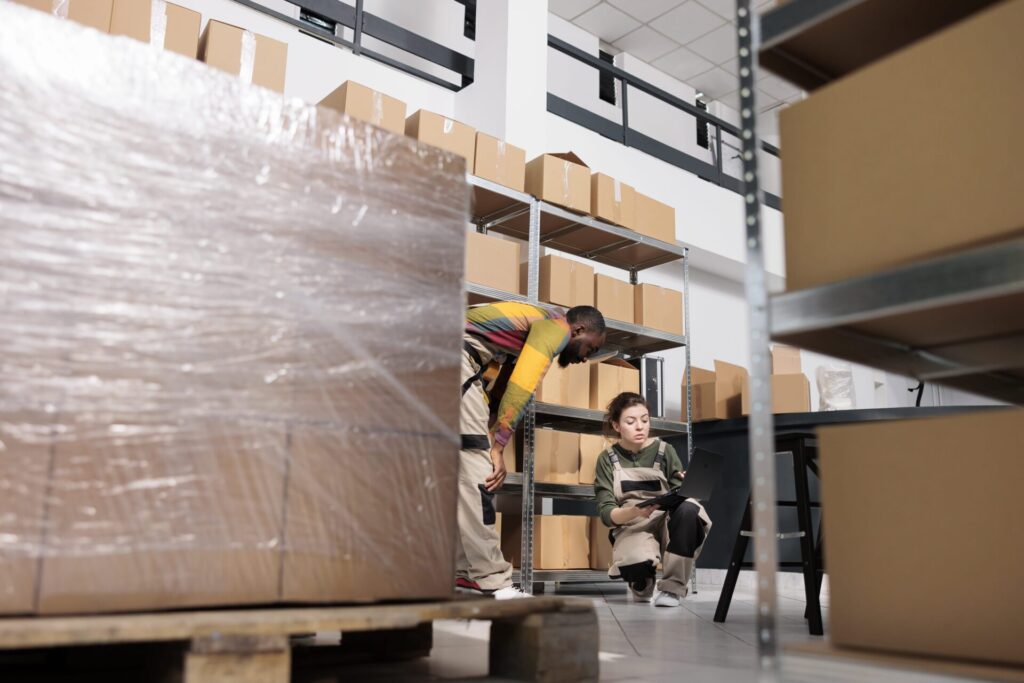
Environmental Considerations
Reusable Packaging Materials
Sustainability is top-of-mind for many businesses:
- Recycled Cardboard: High post-consumer content reduces environmental impact.
- Returnable Crates or Totes: If you regularly ship to the same partner, they can return containers for reuse.
Optimizing Packaging for Sustainability
Even small changes like switching to biodegradable fillers or reducing box sizes can lower your carbon footprint. Bonus: Eco-friendly policies often resonate well with customers, giving you a competitive advantage.Ć
Common Packaging Mistakes and How to Avoid Them
Overhang and Improper Weight Distribution
Placing too large boxes on a standard 48×40 pallet often leads to overhang. You risk:
- Impact Damage: The overhanging edge is vulnerable to bumps.
- Unstable Loads: Reduced surface contact can cause tipping.
Always choose pallets that match or exceed your largest box dimensions to avoid wasted space or precarious overhang.
Insufficient Labeling or Missing Paperwork
Nothing frustrates carriers more than unlabeled freight:
- Missed Deliveries: The shipment might end up at the wrong terminal or be delayed in transit.
- Billing Errors: If the carrier can’t identify the shipper or consignee easily, they could apply incorrect freight classes or charges.
Double-check that every pallet has visible, water-resistant labels, and keep copies of your Bill of Lading (BOL) and packing list handy.
Working with Carriers and 3PLs
Communicating Special Handling Instructions
Inform your carrier or third-party logistics (3PL) partner about:
- Fragile Items: So they load and offload pallets carefully.
- Hazardous Materials: Mandatory for compliance with regulations.
- Appointment Scheduling: If the receiver operates limited hours or requires advanced notice.
Setting Clear Expectations in Contracts
If you have recurring LTL shipments, consider negotiating a contract with your carrier or 3PL, outlining:
- Agreed Packaging Standards: They know what to expect, and you maintain consistent quality.
- Liability Clauses: Ensuring both parties understand who’s accountable if damage occurs due to packaging or handling issues.
Conclusion
Effective LTL freight packaging boils down to two key principles: protection and efficiency. Your goods must be shielded from multiple handling points, shifting loads, and potential forklift bumps, all while minimizing dimensional weight costs. By picking the right pallets, stacking methodically, and securing loads with high-quality wraps or straps, you set yourself up for smooth, damage-free deliveries.
It’s easy to assume packaging is an afterthought, but in the LTL world—where cargo might hop between trucks and terminals—how you package freight can be as important as what you’re shipping. Implementing these best practices ensures your products reach customers intact, upholds your brand’s reputation, and keeps your bottom line in check.
How useful was this post?
Click on a star to rate it!
Average rating 0 / 5. Vote count: 0
No votes so far! Be the first to rate this post.