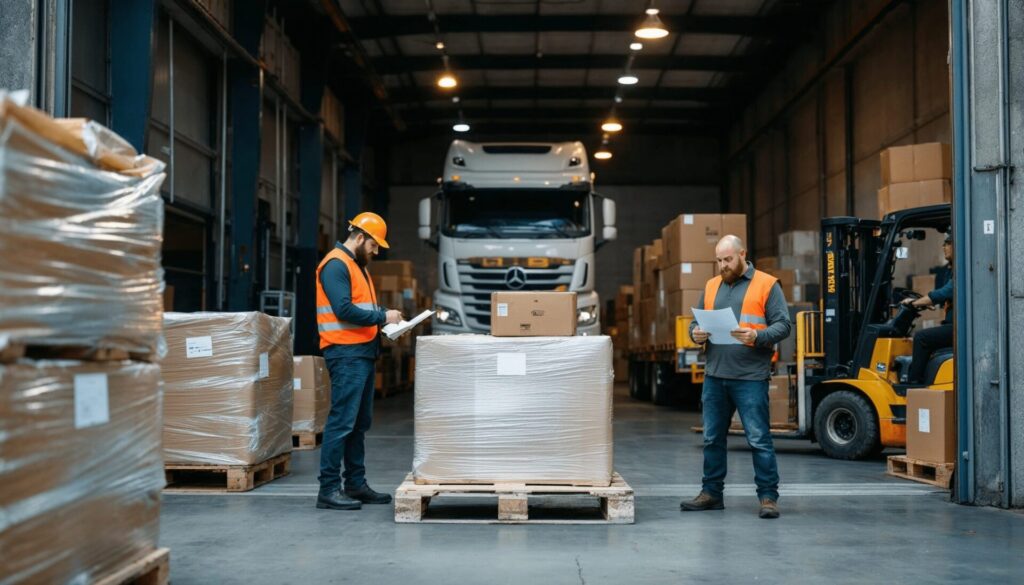
5 Common Mistakes in LTL Freight Shipping
Less Than Truckload (LTL) freight shipping has become a go-to solution for businesses looking to move moderate volumes of goods without paying for an entire truck. By consolidating multiple smaller shipments into a single trailer, LTL carriers allow businesses to share space and cut costs—a win-win for both shippers and carriers.
Yet despite its advantages, LTL shipping also comes with unique challenges. Sending multiple partial loads on the same truck invites possible issues such as handling errors, inaccurate billing, and delays. Below, we’ll examine five of the most common mistakes people make when using LTL freight—and, more importantly, how you can avoid them. Whether you’re a shipping novice or a seasoned pro, understanding these pitfalls can save you time, money, and plenty of headaches down the road.
Introduction to LTL Freight
Why LTL Is Popular for Small and Mid-Size Shipments
The primary draw of LTL shipping is efficiency. Rather than filling a single truck with one company’s cargo, carriers load freight from multiple shippers heading toward the same general region. This setup lets small and mid-sized businesses ship more regularly, so they don’t need to wait until they have a full truck’s worth of goods. If your products range from a few boxes to several pallets—anywhere between 150 and 15,000 pounds—LTL shipping is likely a strong fit.
The Cost-Effectiveness of Sharing Truck Space
When you use LTL, you’re essentially paying for the percentage of trailer space you occupy. This “pay for what you need” model avoids the steep cost of underused truck space if you can’t fill it completely. It also reduces the number of trucks on the road, which can translate into fewer carbon emissions overall—a plus for the eco-conscious. However, the cost-effectiveness hinges on providing precise shipment details and using the correct freight class, which brings us to the first big mistake on our list.
Mistake #1: Inaccurate Shipment Details
Underestimating Weight and Dimensions
One of the easiest (and costliest) mistakes you can make is giving the carrier inaccurate dimensions and weight. If your freight weighs more than declared or takes up more space than you reported, the carrier can reweigh or reclassify your shipment. This often triggers additional fees, late invoices, and headaches you could’ve dodged by accurately measuring from the start.
- Use a Freight Scale: Home or small-office scales might not be sufficient for larger shipments.
- Measure Thoroughly: Include the pallet, crates, and any packaging material in the total dimensions.
Consequences of Incorrect Freight Class
Freight class is primarily determined by density, stowability, handling, and liability. If you claim a lower freight class to save money but the carrier finds otherwise, expect an expensive reclassification. Conversely, if you overshoot the class, you’ll end up overpaying. The moral? Get your class right the first time by calculating density accurately and consulting the NMFC (National Motor Freight Classification) codes.
Mistake #2: Poor Packaging and Labeling
Risks of Damaged Goods
Most LTL loads get moved multiple times—from the initial pickup to regional terminals, cross-dock facilities, and finally the end destination. Every extra touchpoint increases the chance of damage. If your packaging is weak or your items aren’t securely loaded on pallets, you risk broken goods, refused deliveries, and ultimately lost revenue or unhappy customers.
Palletizing Best Practices
- Choose Quality Pallets: Sturdy, undamaged pallets reduce the risk of cargo collapse.
- Stack Strategically: Heavy items at the bottom, lighter or fragile items on top.
- Wrap Tightly: Secure goods with stretch wrap or banding to prevent shifting.
- Label Clearly: Make sure each pallet or box has legible addresses, “Fragile” markings if needed, and orientation labels (like “This End Up”) to guide handlers.
Effective palletizing and labeling minimize confusion at transfer points and help ensure your cargo arrives intact.
Mistake #3: Overlooking Accessorial Services
Liftgate, Inside Delivery, and Limited Access Locations
Not all business locations have the luxury of a loading dock. If the driver arrives and discovers you need a liftgate or inside delivery—services you didn’t specify—this can add unexpected fees to your final invoice. Other scenarios like residential areas, construction sites, or farms may also require special handling known as “limited access,” which often comes with a surcharge.
Unexpected Charges and Delivery Delays
Failing to mention these details can do more than just rack up extra costs; it can also delay your delivery schedule. If a truck arrives without the right equipment, you’ll have to reschedule or wait for a different vehicle to come equipped with what you need. To avoid last-minute curveballs, be upfront about your site’s access requirements and the necessity for special equipment.
Mistake #4: Failing to Compare Carriers and Rates
The Downside of “One-Carrier” Reliance
Staying loyal to a single carrier might feel like a comfortable routine, but it can lead to overpaying. Rates differ widely among LTL providers, depending on factors like route density, terminal locations, and regional coverage. While loyalty can sometimes get you better terms, you might miss out on competitive offers that fit your shipment volume or schedule better.
How Brokers and 3PLs Can Help
If you find it time-consuming to request quotes from multiple carriers, consider partnering with a freight broker or a third-party logistics (3PL) provider. They often have relationships with various carriers and can quickly compare rates, negotiate on your behalf, and offer additional logistics services. This can simplify your shipping process and potentially save you money—so long as you find a trustworthy partner with a strong track record.
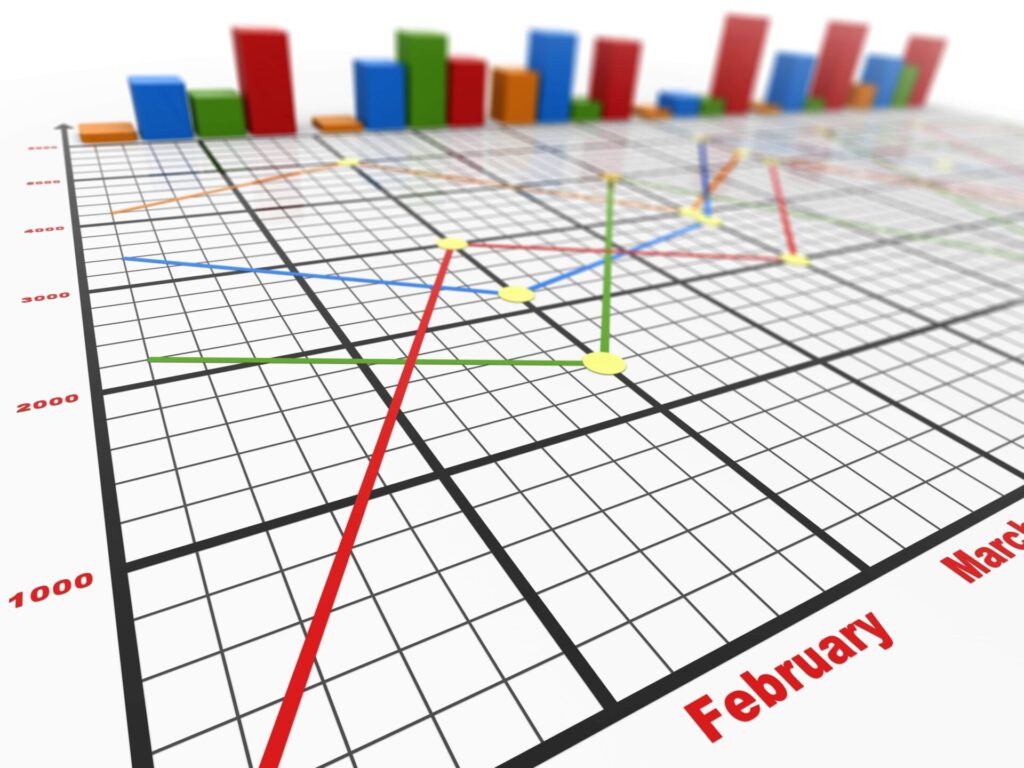
Mistake #5: Neglecting Proper Documentation
Importance of a Correct Bill of Lading (BOL)
The Bill of Lading is the contract between the shipper and the carrier. It outlines exactly what’s being shipped, where it’s headed, how much it weighs, and who is responsible for payment. Omitting details or making errors here can lead to:
- Billing Discrepancies: If the declared weight or freight class is wrong, you’ll get hit with reclassification fees.
- Misdelivery: An incorrect address can send your shipment to the wrong terminal.
- Claims Issues: If there’s damage and your BOL is incomplete, filing a claim becomes more complicated.
Double-check the BOL before the driver arrives and ensure it aligns with the carrier’s system. Clear, accurate documentation is your best defense against billing or delivery conflicts.
Claims and Liability Issues
If freight gets lost or damaged, you’ll likely need to file a claim. Missing or inaccurate documentation can weaken your case. Keep copies of the BOL, packing lists, and any relevant communications in a safe place—you’ll need them to support your claim and possibly to prove the carrier’s liability. Some carriers have tight deadlines for filing claims, so the sooner you can submit the correct paperwork, the better.
The Role of Communication in Avoiding Mistakes
Strong communication is the glue that holds each step of the shipping process together. Establish a clear line of dialogue with your carrier and any intermediaries (like brokers or 3PLs). Confirm that they have the correct details—freight weight, pickup and delivery addresses, additional services needed—well before the shipment date. If anything changes at the last minute, let your carrier know immediately to avoid costly re-deliveries or re-bookings.
Coordination with Carriers and Shippers
- Early Notifications: If your warehouse has limited hours or your loading dock is out of commission, give your carrier a heads-up.
- Regular Check-Ins: A quick phone call or email can prevent a big misunderstanding about scheduling or freight classification.
- Driver Instructions: If the driver needs special directions or contact info, communicate that upfront—this is especially helpful in remote or hard-to-find locations.
Real-Time Tracking and Updates
Many LTL carriers now provide real-time shipment tracking. Leverage these tools to keep tabs on your freight’s whereabouts. If you spot a delay or route deviation, you can proactively alert your customer or receiver. This transparency and responsiveness can bolster your credibility and keep everyone on the same page.
Technology Tools to Streamline LTL Shipping
Modern logistics tech can automate many of the tasks that lead to human error. Freight management software and online rate-quote tools let you input shipment details once and retrieve multiple carrier offers within minutes. They can also track your freight, flag potential errors (like suspiciously low weights), and help you manage documentation.
Freight Management Software (FMS)
- Centralized Data: Store dimensions, freight class, and historical shipment records in one place.
- Automation: Schedule pickups and print shipping labels with a few clicks.
- Analytics: Run reports on your shipping costs, claims, and transit times to spot trends.
Automated Quoting and Comparison Tools
By entering your shipment’s dimensions, weight, origin, and destination into a single platform, you can quickly compare rates from multiple carriers. This method not only saves time but also reduces the likelihood of forgetting key details that might alter your quote. Once you find a competitive rate, booking is often just a click away.
Packaging and Palletizing Done Right
Since multiple stops and transfers are almost inevitable in LTL, your packaging strategy becomes critical.
Cushioning Strategies for Fragile Goods
- Use Quality Packing Material: Bubble wrap, foam inserts, and sturdy corrugated boxes can safeguard fragile items.
- Double-Boxing: Placing an already packed item in a slightly larger box, with cushioning in between, adds an extra layer of protection.
- Separation: Keep heavy items away from delicate objects to avoid accidental crushing.
Labeling Pallets for Quick Identification
Clear labels ensure that your items land on the correct truck during every cross-dock. Use weatherproof labels when possible, and include key details like your company name, the destination address, and any special instructions. If you handle multiple shipments at once, color-coding can speed up sorting and minimize mix-ups.
Best Practices for Accurate Freight Classing
Freight classing isn’t just about calculating density. You also need to consider stowability (can it be stacked easily?), handling (is it fragile or hazardous?), and liability (is it high-value or easily damaged?).
Density Calculations and NMFC Codes
Calculate the cubic feet of your shipment by multiplying length, width, and height in inches, then dividing by 1,728 (the number of cubic inches in a cubic foot).
Density (lbs/ft³) = (Weight of Freight in lbs) ÷ [(Length in inches × Width in inches × Height in inches) ÷ 1728]
Look up the NMFC code that best fits your item. If you’re shipping something unusual or mixed items on the same pallet, consult with the carrier or an NMFC guide to ensure you select the correct class.
Working With Carriers to Verify Class
When in doubt, ask your carrier for assistance. Some carriers can provide a quick verification if you supply product details and packaging specifics. This step might prevent a reclassification fee later. Remember, honesty is the best policy—trying to sneak into a cheaper class can backfire if the carrier notices inconsistencies.
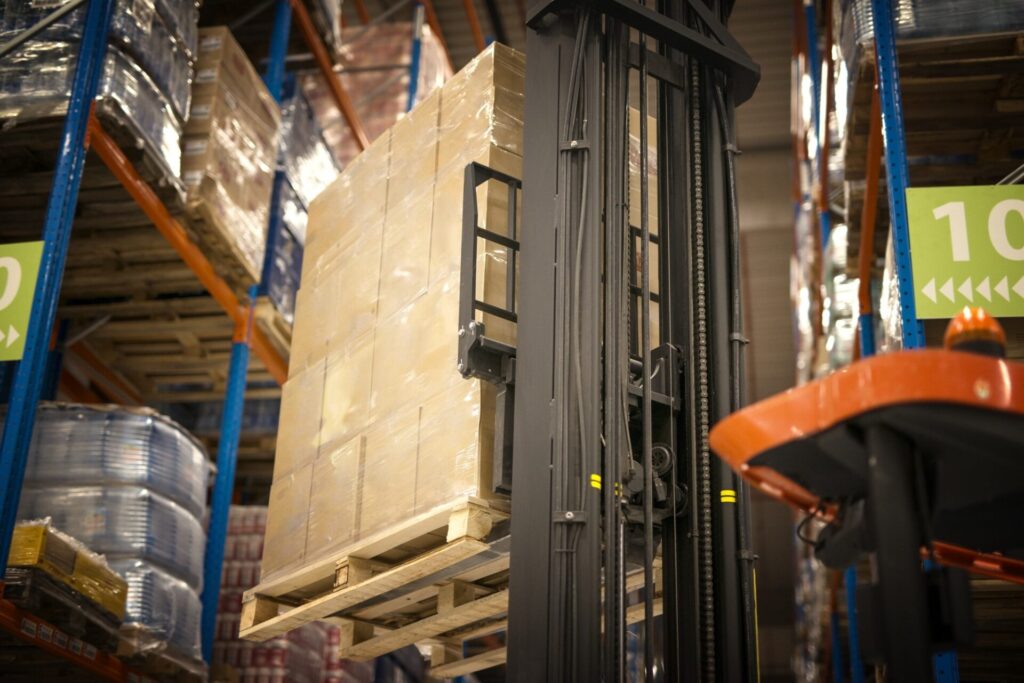
How to Factor in Accessorial Fees
Stickershock often comes from neglected or unexpected accessorial charges. If you plan ahead, you can either minimize or accurately budget for these costs.
Identifying Delivery Constraints Early
- Elevators or Stairs: If you need inside delivery above ground level, mention that upfront.
- Restricted Hours: Some businesses, like schools or hospitals, have strict receiving windows.
- High Security: Government buildings and military bases may require extra clearance or driver identification.
Being transparent about these constraints lets the carrier plan effectively and quote you properly—reducing the chance of being blindsided by a hefty bill.
Scheduling for Efficiency and Cost Savings
When possible, schedule pickups or deliveries during standard business hours and ensure you have the necessary equipment or personnel on-site. Avoid last-minute changes like moving the delivery to a residential address or requesting a weekend drop-off. The more consistent and predictable your shipping process is, the more likely you’ll lock in stable, lower rates.
Comparing Quotes and Negotiating Rates
LTL shipping is competitive, and carriers want your business. You have more leverage than you might think—especially if you’re shipping regularly or can consolidate freight along specific routes.
Volume Discounts and Contract Pricing
If you consistently ship to the same region or commit to a certain number of shipments each month, many carriers will offer volume-based pricing or a contract rate. Even small businesses can snag discounts if you show a history of consistent shipping.
Timing Your Shipments
Peak shipping periods—like during certain holiday seasons—can drive up rates. Whenever possible, plan shipments outside of high-demand times, or be flexible with pickup and delivery dates. Keeping an eye on market trends and fuel costs can also help you negotiate a better deal.
Mitigating Risk and Handling Claims
No matter how well you plan, issues like damage or loss can still happen. Knowing how to handle them efficiently is crucial.
Inspecting Shipments Upon Delivery
Always check for visible damage before signing off on the delivery receipt. If something looks amiss—like wet packaging, torn shrink wrap, or dented boxes—note it on the Bill of Lading. Photos are your best friend here; snap pictures of any damage, including the packaging. This documentation can be invaluable if you need to file a claim.
Documenting Damage and Filing Claims Promptly
Many carriers have tight deadlines for damage claims—some as short as five to 15 days. Delaying a claim can result in denial. Even if you’re unsure whether the damage is extensive, filing early is better than missing the window. Keep all emails, BOL copies, photos, and inspection reports in a single folder so you can present a clear case to the carrier.
Conclusion
LTL freight shipping remains one of the most flexible and cost-effective ways for businesses to move moderate-sized goods. By paying only for the space you need, you can efficiently deliver products to customers without the overhead of a full truckload. However, the same factors that make LTL shipping economical—multiple pickup points, shared trailer space, and variable routes—also pave the way for mistakes.
The top five errors—providing inaccurate shipment details, neglecting proper packaging, overlooking accessorials, sticking to a single carrier, and ignoring proper documentation—can significantly inflate your expenses or delay deliveries. Fortunately, each of these pitfalls is avoidable with a bit of diligence. Carefully measure and weigh your freight, label pallets correctly, verify needed services in advance, explore multiple carriers, and double-check your documentation.
When done right, LTL freight shipping can streamline your logistics, reduce your carbon footprint, and boost your bottom line. By learning from these common mistakes, you’ll not only save yourself from unnecessary costs but also build stronger relationships with carriers and customers alike. Keep these tips in mind for your next shipment, and you’ll be on your way to a more efficient, headache-free LTL experience.
How useful was this post?
Click on a star to rate it!
Average rating 0 / 5. Vote count: 0
No votes so far! Be the first to rate this post.