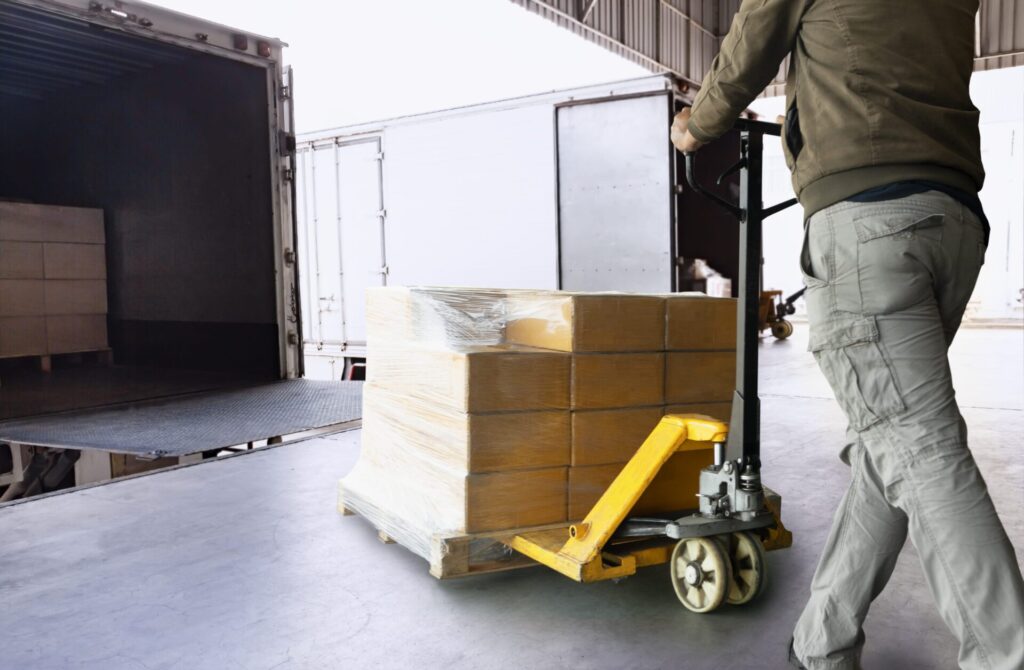
Preparing Pallets for LTL Freight Shipping
When shipping via Less Than Truckload (LTL), you’re combining your freight with other customers’ shipments on the same trailer. While this strategy can lower costs, it also raises the risk of damage or misrouting if your pallets aren’t prepared properly. From picking sturdy pallets to labeling them with clear instructions, each step in palletizing your cargo ensures a smoother, more reliable LTL shipping experience.
This guide delves into the best practices for assembling pallets in an LTL context, covering how to distribute weight evenly, wrap goods securely, and mitigate damage risk despite multi-stop journeys. Whether you’re shipping a few pallets monthly or managing weekly loads, optimizing your pallet prep can significantly reduce claims, expedite unloading, and maintain strong partnerships with carriers.
Introduction
Why Proper Pallet Preparation Matters
Multi-stop LTL shipping often subjects your pallets to repeated loading and unloading at cross-dock facilities. If your freight is poorly secured, loosely wrapped, or has protruding corners, you raise the chance of toppling boxes or forklift damage. Well-prepared pallets not only arrive intact but also expedite carrier handling—improving on-time performance and lowering administrative headaches from claims or rework.
Common Pitfalls of Poor Palletization
Pitfalls include:
- Overhang: Boxes that jut out from pallet edges can be easily crushed.
- Shaky Stacks: Mixed box sizes without a stable base can collapse in transit.
- Inadequate Stretch Wrap: Insufficient or sloppily applied wrap leads to shifting, unbalanced loads.
When these issues appear, carriers may label shipments as high-risk, imposing extra fees or refusing loads entirely.
Selecting the Right Pallet
Standard Pallet Dimensions and Materials
A 48″ x 40″ wooden pallet—often called the GMA (Grocery Manufacturers Association) pallet—is a de facto standard in North America. Check that slats and stringers are sturdy, with no missing boards or major cracks. Alternatively, plastic pallets are lighter, more durable, and resist moisture—useful for water-sensitive goods. While typically more expensive, plastic pallets may reduce damage if your LTL shipments often see rough handling.
Checking Pallet Condition for Safety
Worn or rotted wood planks can break mid-transit, toppling your stacked items. Always test a pallet’s load capacity before stacking heavy boxes. If your pallet is sagging or nails are loose, discard it rather than risk shipping fiascos. Carriers might reject shipments on obviously compromised pallets, forcing you to re-palletize on the spot.
Weight Distribution and Load Stability
Centering Heavy Items for Balance
Uniformly dispersing weight across the pallet is key: heavier or denser boxes go on the bottom layer to maintain a low center of gravity. If you place heavy goods off-center, the pallet can tilt or shift in transit. Ensure weight does not exceed recommended pallet capacity—commonly around 2,000–3,000 lbs for standard wood pallets (though some are rated higher).
Layering and Interlocking Boxes
Stack boxes in neat layers, ideally with each layer oriented 90° from the one below (like brick-stacking). This interlocking pattern reduces column-based weak points, where one stack could tip if it’s all aligned in the same direction. If your boxes differ in size, fill gaps with smaller boxes or padding—minimizing voids so items don’t shift.
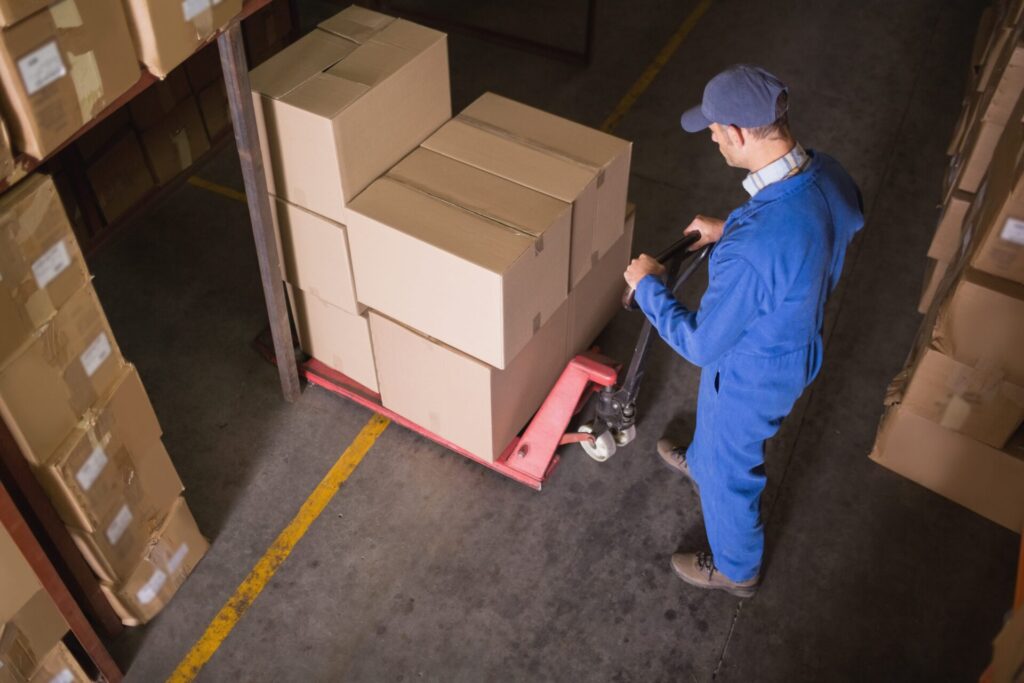
Protective Wrapping and Securing
Choosing Stretch Wrap vs. Banding
- Stretch Wrap (Shrink Wrap): Commonly used for general loads. Wrap from the pallet base up over the top, maintaining tension. This encloses items together as a unified block. If you ship items requiring extra rigidity, combine stretch wrap with corner boards.
- Banding or Strapping: Plastic or metal bands around the pallet’s perimeter may supplement stretch wrap for heavier goods. This method compresses boxes, helping them stay in place. Ensure band tension is correct; too tight can crush items, too loose is ineffective.
Using Edge Protectors and Corner Boards
Corrugated cardboard corner boards fit along pallet edges—key for stabilizing top layers and preventing banding from biting into boxes. Edge protectors can also reinforce box corners that are prone to denting. Such protective inserts are vital if your commodity is brittle or easily scuffed.
Labeling and Marking
Clear Address and PRO Number Placement
Each pallet needs a shipping label or BOL reference that is highly visible on multiple sides. List the origin, destination, and relevant reference or PRO number the carrier issues for tracking. If you rely on barcodes or QR codes, ensure they’re not obstructed by stretch wrap glare. Redundant labels minimize the risk of misrouting, since carriers confirm details at each cross-dock.
Handling Instructions: Arrows, Fragile Stickers
If your items must remain upright or can’t be stacked, add arrows or “This Side Up” warnings on the pallet sides. Mark “Do Not Stack” or “Fragile” if applicable. LTL staff handle thousands of shipments daily, so large, bright symbols help them load or unload responsibly.
Handling Delicate or Odd-Shaped Items
Using Crates or Specialized Padding
High-value or fragile goods, such as electronics or glass, often benefit from wooden crates or interior foam inserts. Although crates cost more, they significantly diminish claims from breakage or vibration damage. If your items have irregular protrusions, custom foam corner braces help keep corners or edges safe during forklift movement.
Blocking and Bracing Tactics
When shipping multiple dissimilar items on one pallet, use blocking (like additional boards) to partition heavier objects from lighter ones. This prevents heavier items from sliding or toppling onto fragile boxes. Additionally, bracing boxes with corrugated inserts keeps them snug, cutting down on sideways shifting.
Pallet Height and Overhang Considerations
Avoiding Overhang to Prevent Damage
If boxes hang off the pallet edges, forklift forks or adjacent freight can easily crush or tear them. Overhang also signals carriers you might have miscalculated dimension, potentially fueling reweigh or reclass fees. Keep all items squarely within the 48″x40″ footprint (or any standard size used) for optimum safety.
Monitoring Height for Carrier Compliance
Carriers or terminals often have max height constraints (like 84″ for certain routes) to stack double pallets in a trailer. If your load surpasses typical height, they might treat it as oversize or reposition it for safer stowage, sometimes adding surcharges. Confirm your pallet’s final stacked height before shipping, so you’re not blindsided by extra fees.
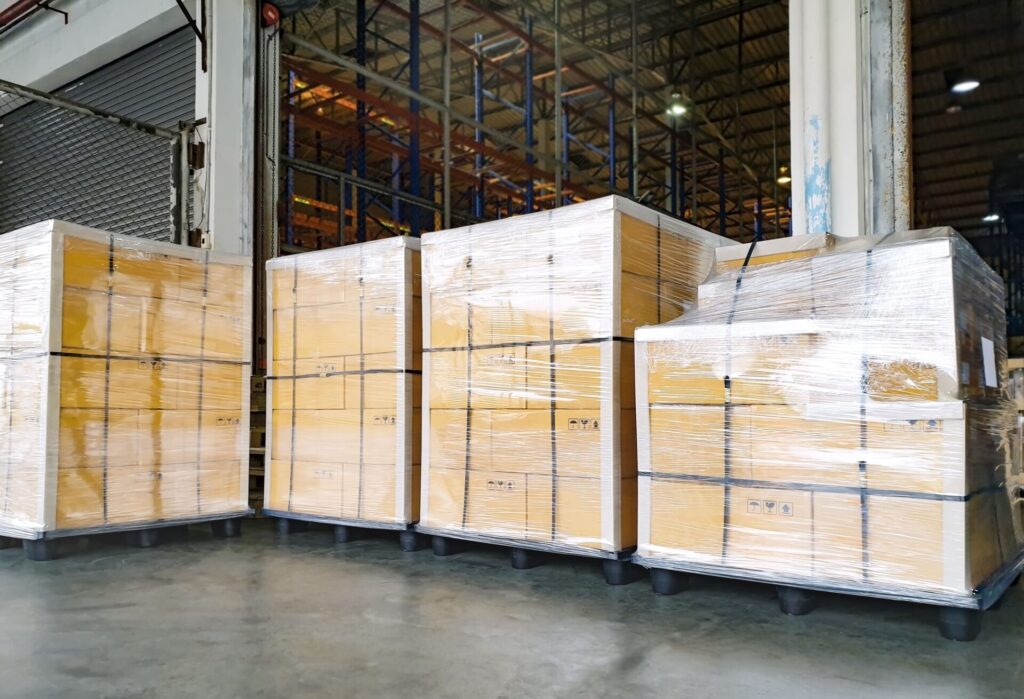
Tips for Efficient Loading and Unloading
Orientation for Forklift Access
Arrange your pallet’s heavier sides or bullet points so a forklift can approach from multiple angles. Standard GMA pallets have forklift openings on all four sides, but if you place loads that block forklift entry, staff may forcibly shift items or refuse the pallet. Also, keep labeling or fragile symbols visible from the forklift operator’s vantage point.
Grouping Pallets by Destination
When shipping multiple pallets, group them in the staging area based on carrier or final location to save loading time. Carriers can retrieve them quickly, verifying addresses with scanning equipment. This streamlined approach also helps avoid accidental shipping mix-ups if multiple shipments coincide at your dock.
Quality Checks Before Shipment
Inspecting Banding Tension and Wrap Tightness
A last-minute check: Are bands snug? Is the shrink wrap layered enough around corners and the pallet base? If you can nudge boxes around, add an extra pass of wrap. Confirm the pallet deck boards aren’t splitting, which can fail once lifted onto a trailer. Better to rewrap or swap pallets than deal with a damage claim.
Documenting Conditions with Photos
Taking quick phone snapshots of each pallet—front, back, sides—provides a record if the carrier denies liability later. Should a forklift tear your load mid-transit, you’ll have visual proof it left in perfect shape, backing your damage claim. This minimal time investment often pays off in fast claim settlements.
Conclusion
Preparing pallets for LTL freight isn’t just about stacking boxes and applying wrap. By thoughtfully selecting sturdy pallets, balancing weight, using protective wrap and labels, and verifying dimensions align with carrier standards, you drastically reduce the chance of damage, reweigh fees, or shipping disputes.
Remember, LTL shipments typically endure multiple handling touches—each cross-dock or trailer swap amplifies risk. Meticulous pallet preparation ensures your goods survive those transitions intact. From a simple forklift-friendly orientation to specialized crating for fragile items, each measure fosters smoother journeys, fewer claims, and better operational flow. Armed with these best practices, your LTL shipments can sail through any hub, unscathed and on time.
How useful was this post?
Click on a star to rate it!
Average rating 0 / 5. Vote count: 0
No votes so far! Be the first to rate this post.