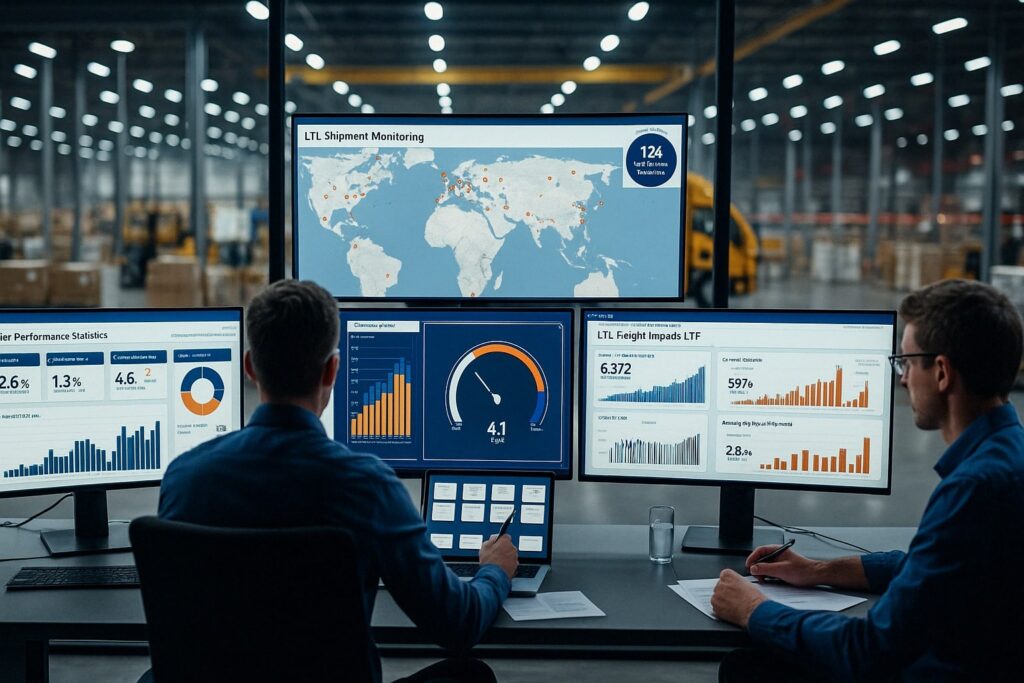
How LTL Freight Impacts Supply Chains
In supply chain management, every shipment—whether large or small—can significantly affect the efficiency and profitability of logistics networks. Less Than Truckload (LTL) freight stands out as a practical solution for shippers that need to move partial loads more frequently, without waiting to fill an entire trailer. Yet while LTL offers flexible scheduling and shared costs, it also weaves added complexity into each link of the supply chain.
This expanded guide uncovers how LTL shipping shapes inventory management, carrier relationships, and cost structures, influencing the overall resiliency and responsiveness of modern supply chains. From analyzing handling challenges and cross-docking to leveraging data-driven strategies and robust packaging methods, we’ll see how LTL choices can either supercharge or hamper your logistics performance.
Introduction
The Rise of LTL in Modern Logistics
As e-commerce fuels demand for quicker deliveries and smaller order sizes, businesses often ship partial loads on short notice. LTL carriers have responded by refining schedules, consolidating shipments, and offering a range of specialized services. This shift allows even small to mid-sized enterprises to match larger competitors’ shipping frequency, broadening market reach.
Balancing Efficiency with Complexity
On one hand, splitting a trailer among multiple shippers reduces costs and optimizes capacity usage. On the other, managing multiple shipments in a single route or cross-dock introduces extra steps—like sorting, labeling, and potential reclassifications. The net effect can push transit times higher or require vigilant oversight to ensure no cargo gets misdirected or damaged.
The Basics of LTL Shipping
Defining LTL and Its Role
“Less Than Truckload” covers freight that doesn’t occupy an entire 48- or 53-foot trailer. Usually, these shipments weigh 150–15,000 pounds, though carriers set various maximum thresholds. Each shipper pays only for the space (or weight) used, sharing overall costs such as fuel, driver wages, and equipment. This model suits regular, smaller shipments going to multiple locations, from retail restocking to B2B parts distribution.
Core Differences from FTL
In a Full Truckload (FTL) scenario, one shipper controls the entire trailer, typically ensuring a single pickup, direct route, and minimal handling. By contrast, LTL merges multiple loads, each with unique origins and destinations, making multi-stop routes and multiple cross-docks standard. While it’s cost-effective for partial loads, it also raises the risk of delays, damage, or scheduling conflicts if shipments aren’t meticulously planned.
Key Ways LTL Shapes Supply Chain Dynamics
Enhancing Flexibility and Frequency
Traditional supply chains often revolve around bulk orders or monthly shipping cycles. LTL shipping shrinks this cycle—companies can dispatch loads weekly or even daily, aligning with just-in-time replenishment needs. As a result:
- Less Stock is stored in warehouses, lowering overhead.
- Faster Responses to spikes in demand or new customer orders become feasible.
Supporting Just-in-Time and Demand-Driven Strategies
High inventory levels tie up capital and risk obsolescence or spoilage. LTL’s frequent partial-load approach underpins lean manufacturing processes. By synchronizing shipments with production or sales forecasts, supply chains can minimize carrying costs and respond promptly if demand shifts.
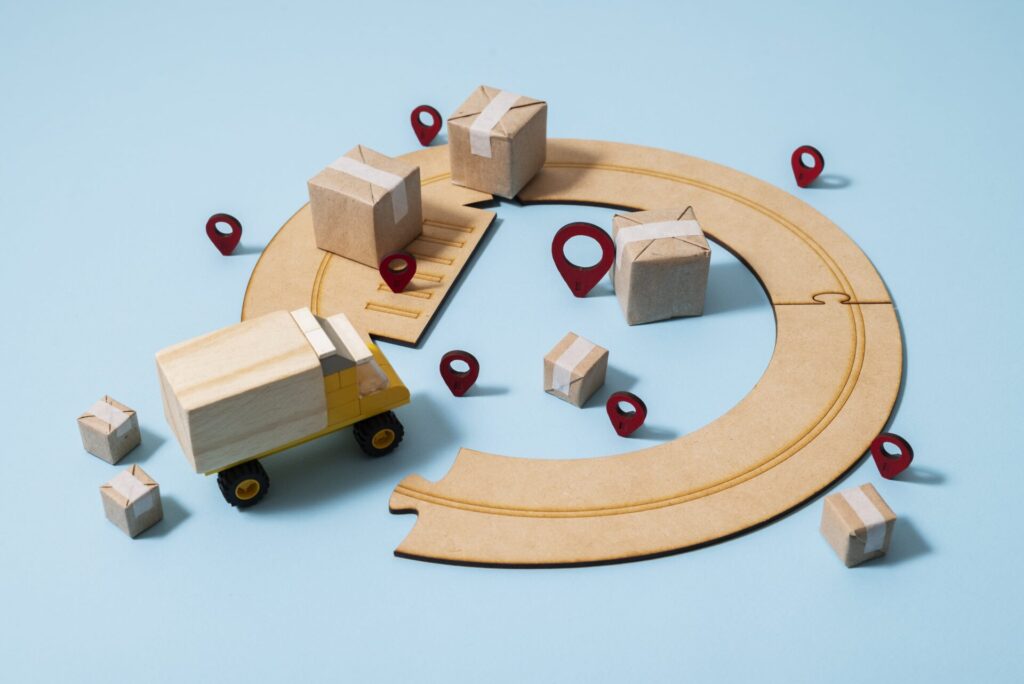
Multiple Touchpoints and Transit Times
Cross-Docking’s Pros and Cons
Many LTL carriers rely on hub-and-spoke networks. Goods converge at a central terminal, get sorted by destination, and move on. Benefits include better trailer fill rates and often lower shipping costs if consolidated effectively. However, each loading/unloading event adds a potential point of damage or misrouting.
Risk of Delays from Terminal Handoffs
If a terminal or cross-dock location experiences staff shortages or mechanical breakdowns (e.g., forklift issues), shipments can pile up. LTL lines typically run on tight windows; any glitch can push deliveries to the next available run. Shippers reliant on strict, time-definite arrivals might see LTL as a potential risk factor unless they choose carriers offering guaranteed service.
Cost Considerations in the Supply Chain
Per-Pound or Dimensional Pricing
Carriers typically set LTL rates based on freight class, weight, and distance. Some also factor in “cube” (dimensional weight) if volume is significant compared to actual weight. For supply chain budgeting, analyzing these pricing schemes is crucial—especially if you frequently ship lightweight but bulky products that might be penalized under dimensional pricing.
Impact of Fuel Surcharges and Accessorials
Fuel surcharges fluctuate monthly or weekly as diesel prices shift. Meanwhile, specialized services—such as limited access pickup, liftgate usage, or inside delivery—trigger additional fees. Overlooking these can blow up your shipping budget or lead to disputes when reconciling invoices, complicating financial forecasting and inventory costing.
Packaging and Handling Requirements
Reducing Damage with Palletizing Techniques
In LTL shipping, cargo may be moved several times. Robust palletizing helps cargo withstand repeated forklift handling. Key tips include:
- Heavier Items on lower pallets or at the bottom of each pallet stack.
- Even Weight Distribution—avoid leaning pallets or overhang.
- Protective Wrapping and edge protectors to brace delicate corners.
Aligning Product Sensitivity with Carrier Selection
Not all carriers handle fragile or temperature-sensitive freight equally well. Some excel in specialized shipping—like a blanket-wrap approach for furniture or reefer trucks for perishables. Matching your product’s nature to the right LTL partner fosters smoother handling, fewer claims, and better brand consistency.
Inventory and Warehouse Management
Shorter Lead Times vs. Increased Frequency
Embracing LTL typically means multiple smaller shipments spread across the month. This helps keep fresh inventory for your end customers, trimming large storage commitments. However, each new shipment requires scheduling, packaging, and potential overhead in your shipping department. Balancing these factors is key to ensuring timely deliveries without over-burdening staff or carriers.
Consolidation and Pool Distribution Approaches
Companies shipping to numerous nearby destinations can leverage pool distribution, funneling goods to a single hub before distributing them. LTL carriers specializing in certain regions might group shipments from multiple customers to fill a trailer heading to a “pool point,” then dispatch local trucks for the final leg. This method can reduce individual cross-docks, accelerating transit and cutting costs.
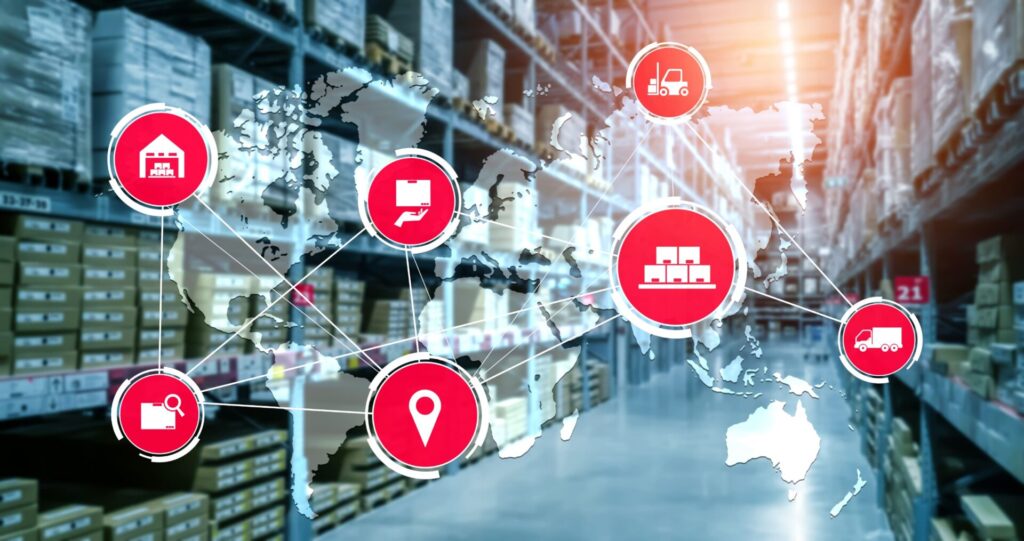
Leveraging Technology for Improved Visibility
TMS Solutions and Real-Time Tracking
Transportation Management Systems (TMS) unify quoting, booking, BOL generation, and tracking under one platform. By centralizing data, supply chain managers quickly spot potential holdups, track each shipment’s route, and streamline administrative tasks like invoice reconciliation. Real-time or near-real-time GPS-based tracking or status updates improve planning accuracy and reduce last-minute firefighting.
Data Analytics for Lane Optimization
Beyond daily tracking, analyzing historical shipping data across lanes, carriers, seasons, or product lines provides a robust basis for continuous improvements. For instance, if Lane A sees consistent delays or high claims, you might renegotiate with the carrier or switch providers. Over time, these informed adjustments raise delivery reliability and reduce overall costs.
Cross-Border and Global LTL Complexities
Customs Clearance and Documentation
When LTL extends internationally—e.g., shipping from the U.S. to Canada or Mexico—shippers face additional customs paperwork (commercial invoices, certificates of origin, etc.). Inconsistent or incomplete documents trigger border delays, harming lead-time commitments. Collaborating with carriers that have cross-border expertise or employing a customs broker can speed up clearance.
Carrier Partnerships in International Networks
Some domestic carriers maintain alliances with overseas providers for seamless transoceanic LTL. However, each handoff (e.g., from port to local trucking) risks misrouting. Evaluate carriers’ experience, local presence, and familiarity with your commodity’s compliance rules. Achieving stable cross-border shipping rates might involve signing a multi-lateral agreement among multiple carriers.
Risk Mitigation and Insurance
Carrier Liability Limits vs. Actual Cargo Value
Standard LTL liability rarely reflects true product worth—often capping compensation at a few dollars per pound. High-value goods could face significant losses if damaged or stolen. If you’re shipping pricey electronics or specialized parts, additional cargo insurance or declared value coverage closes the gap.
Filing Claims and Handling Disputes
To protect your supply chain, define an internal protocol for:
- Inspecting Freight upon delivery and noting any visible damage on the proof of delivery (POD).
- Photographing and documenting damage for claims submission.
- Acting Quickly: Carriers impose tight claim windows (often under 15 days).
A proactive stance ensures faster payouts and minimal inventory disruption.
Building Collaborative Carrier Relationships
Communication on Scheduling and Forecasting
Shippers with a consistent volume or lane usage can share forecasts with carriers, helping carriers plan capacity. This synergy often yields more stable rates, quicker pickups, and stronger loyalty—critical during capacity crunches.
Continuous Improvement for On-Time Delivery
Regular performance reviews—quarterly or monthly—spot trends like a rising claim ratio or late deliveries. Work with carriers to dissect root causes (insufficient staff, older trailer fleets, route inefficiencies) and tweak processes. This collaborative approach fosters a supply chain built on agility, not just transactional cost haggling.
Conclusion
LTL freight has redefined how modern supply chains function, enabling smaller, frequent deliveries across diverse markets. By balancing multiple handling points, specialized packaging demands, and intricacies around cost structures, LTL can serve as a potent driver of just-in-time inventory, flexible manufacturing, and consistent end-customer satisfaction. However, it demands careful carrier selection, robust technology utilization, and proactive risk management—particularly around claims, potential delays, and specialized cargo needs.
While the path may be complex, the payoff is substantial. Companies who master LTL shipping cultivate supply chains that react nimbly to demand shifts while keeping overhead in check. Ultimately, tailoring an LTL strategy around your unique product mix, shipping lanes, and partner ecosystems can transform a cumbersome logistical segment into a source of competitive advantage.
How useful was this post?
Click on a star to rate it!
Average rating 5 / 5. Vote count: 1
No votes so far! Be the first to rate this post.