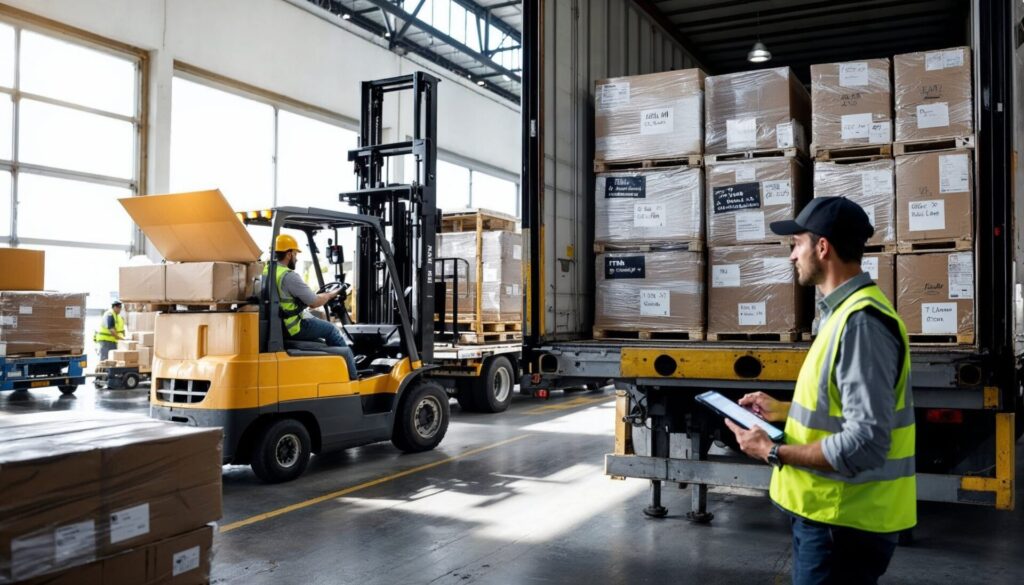
Improving LTL Freight Delivery Times
Balancing affordability with speed is at the heart of Less Than Truckload (LTL) shipping. Although LTL offers cost savings for smaller loads, the trade-off is potential delays stemming from multiple handling points, complex route planning, and unpredictable capacity constraints. Yet, with smart planning and the right strategy, shippers can make the most of LTL while keeping transit times in check.
In this article, we’ll explore the many factors affecting LTL freight delivery speed and examine how you can address them—through better scheduling, streamlined packaging, closer collaboration with carriers, and effective technology solutions. By optimizing each stage of the LTL process, you can reduce transit times and keep customers satisfied, all while maintaining cost efficiency.
Introduction
Why LTL Delivery Speed Matters
LTL shipping appeals to businesses that don’t move enough volume to warrant a full trailer. However, in today’s fast-paced market—where just-in-time manufacturing and e-commerce commitments demand swift deliveries—speed is crucial. Late shipments can mean missed sales opportunities, disappointed customers, and added storage costs. Ensuring timely LTL deliveries can thus become a competitive advantage, supporting better customer satisfaction and healthier bottom lines.
Balancing Cost and Timeliness in Partial Loads
A key challenge lies in reconciling the budget benefits of partial-truck sharing with the desire for faster transit. By nature, LTL carriers merge shipments from multiple shippers, leading to more frequent stops and cross-docking. This can inflate transit times compared to Full Truckload (FTL). However, adopting strategic measures—from selecting experienced carriers to consolidating freight—helps mitigate delays while preserving the fundamental cost perks of LTL.
Understanding Common Causes of LTL Delays
Multiple Handling Points and Cross-Docking
Unlike FTL’s direct route, LTL shipments often pass through multiple terminals, each involving:
- Unloading: Freight is taken off a truck.
- Sorting: Pallets are grouped by next destination.
- Loading: Shipments are reloaded onto another vehicle.
Each touchpoint raises the chance of misrouting, damage, or waiting times—especially if scheduling is tight or communication breaks down.
Seasonal Fluctuations and Capacity Issues
Peak shipping seasons—like the holiday rush or quarterly surges—strain carrier networks, making it harder to secure quick pickups. Carriers might re-route shipments through alternative hubs with available capacity, dragging out transit. Proactive planning and early slot bookings become indispensable when capacity tightens.
Choosing the Right LTL Carrier or Broker
Evaluating Transit-Time Performance
Not all carriers deliver the same level of speed or consistency. Some specialize in regional lanes with rapid turnarounds; others offer extensive national coverage but may face more stops along the way. Reviewing on-time performance metrics, average dwell times, and references from other shippers can shed light on a carrier’s reliability.
The Role of Carrier Reputation and Network Coverage
A carrier’s terminal network shapes how quickly it can move your freight. Dense networks with strategically located hubs often result in fewer delays. Meanwhile, a well-regarded carrier or competent freight broker can expedite load planning, manage re-routes effectively, and resolve issues if problems arise mid-transit.
Planning and Scheduling Your Shipments
Importance of Accurate Lead Times
Overly optimistic schedules—where you underestimate how long it takes to produce or pick your items—lead to rushed pick-ups or missed carrier appointments. Provide carriers with realistic time frames. If your freight is not ready at the declared pickup time, carriers might charge detention or push your shipment to the next day’s route, delaying delivery.
Coordinating Pickup Windows and Dock Hours
Carriers often assign arrival windows (e.g., “between 1:00–4:00 p.m.”) rather than fixed times. By keeping dock staff prepared and having all pallets labeled and staged, you minimize loading delays. Solid planning helps carriers stick to their route schedules and reduces the chance your freight sits in a terminal overnight waiting for another truck.
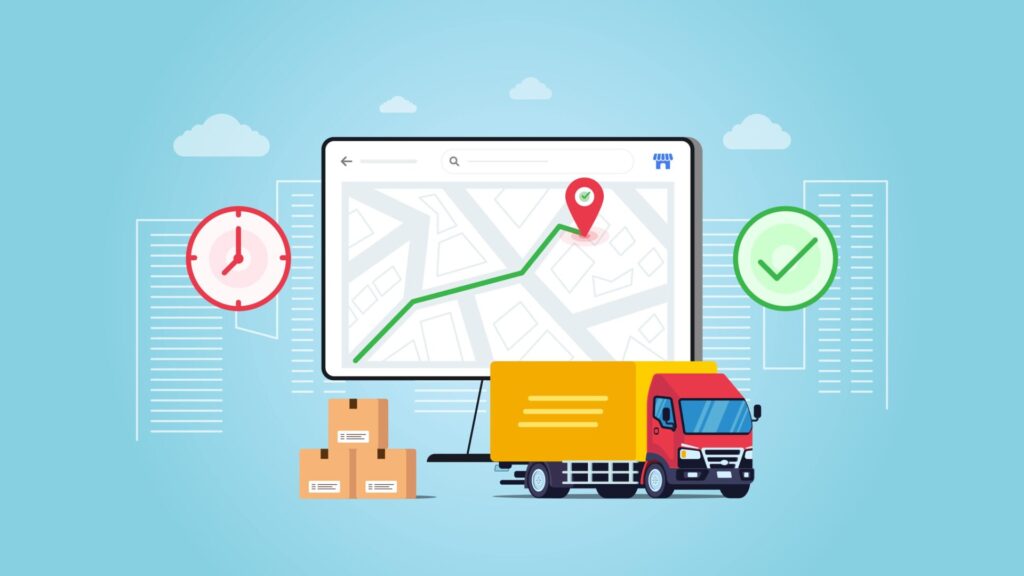
The Impact of Packaging and Labeling on Speed
Palletizing Efficiently to Avoid Rework
Properly palletized freight speeds up cross-docking. If cargo shifts or boxes slide off ill-prepared pallets, carriers must rewrap or re-stack at intermediate terminals, causing unplanned stops. Using corner protectors, secure shrink-wrap, and stable pallets helps cargo flow seamlessly through each handling stage.
Proper Labeling to Prevent Misrouting
Clear, legible labels with:
- Shipper and Consignee Names
- Origin and Destination
- PRO/BOL Reference Numbers
are essential. Even minor labeling errors risk your freight getting mis-sorted, winding up on the wrong truck, or languishing at a terminal for days.
Leveraging Consolidation and Pool Distribution
Reducing Touchpoints by Merging Shipments
If your business sends multiple partial loads weekly, consider consolidating them into fewer but larger LTL shipments. Fewer loads mean carriers handle them less often, lowering re-handling times. This especially helps if your shipments head to similar destinations.
Pool Points for Regional Distribution
Pool distribution merges freight at a central location, then quickly distributes it regionally. By clustering deliveries close together, carriers can run more direct routes. This approach slashes overall transit times and can cut costs, especially if you consistently serve the same geography.
Managing Freight Classes and Documentation
Accurate NMFC Codes for Faster Handling
Carriers often check if your stated freight class matches the physical reality. Misclassification triggers reweighs, reclassifications, or billing disputes, all of which stall your shipment. Precisely listing the correct NMFC code and ensuring your Bill of Lading is consistent can reduce rerouting or administrative holdups.
Preventing Delays by Avoiding Reclassification
When carriers detect inconsistencies—like an incorrect or vague commodity description—they may sequester cargo until the shipper clarifies the class or pays an adjustment. The more you double-check your weight, dimensions, and classification up front, the less likely your freight gets stuck mid-transit.
Communication with Carriers and Consignees
Real-Time Tracking and Status Updates
Many LTL carriers and 3PLs now provide online portals or APIs. By monitoring your shipment’s progress, you can identify potential delays (e.g., weather disruptions) earlier. Proactive communication with the consignee ensures a quick unload upon arrival, preventing missed or rescheduled deliveries.
Proactive Issue Resolution
If you spot a delay—say, your shipment is unexpectedly diverted—contact your carrier promptly. Together, you might expedite final delivery or reroute cargo to a more convenient terminal. Swift action often averts multi-day holdups.
Harnessing Technology for Speed
TMS Solutions and Automated Scheduling
A Transportation Management System (TMS) automates freight booking, consolidates shipments, and compares carrier rates. By centralizing data—like truck availability and lane schedules—a TMS accelerates the planning process, reducing the time freight sits idle waiting for pickup or route confirmations.
Online Tracking Portals and APIs
Carriers that offer real-time or near-real-time tracking feed data into your TMS or an online portal. This visibility:
- Alerts you when your shipment arrives at a terminal.
- Provides updated ETAs, letting your receiving dock plan labor and space.
Facilitates quick adjustments if a route change becomes necessary.
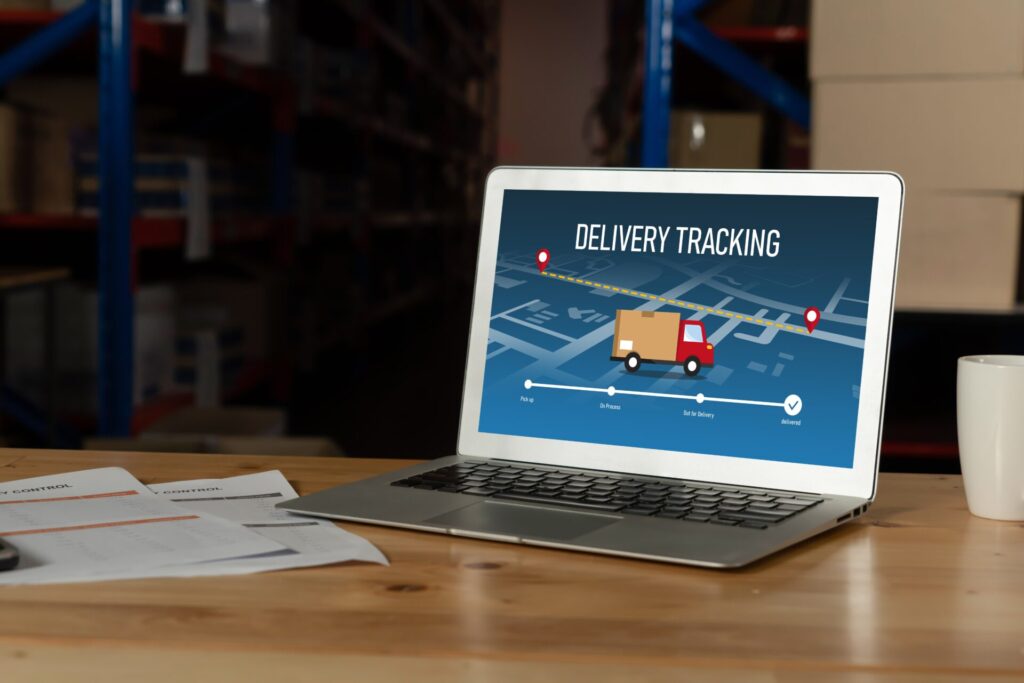
Dealing with Seasonal and Peak Shipping Periods
Booking Early and Slot Reservations
During busy seasons (e.g., holiday peak), carriers face capacity crunches. If you book your LTL shipments last-minute, expect higher rates and extended transit times. Securing your slot in advance, maybe a week or two earlier, often nets more stable times and guaranteed capacity.
Contingency Plans for Capacity Crunches
Even if you plan meticulously, external factors like severe weather or labor strikes can sabotage schedules. Maintaining backup carriers or working with a broker who can pivot to alternative routes ensures your freight doesn’t languish in a congested hub.
Minimizing Accessorial Delays
Liftgate, Inside Delivery, and Appointment Fees
Services like a liftgate at delivery or inside pickup can slow the process if carriers weren’t alerted beforehand. If your consignee needs inside delivery, note it early. Otherwise, carriers might show up unprepared, leading to reattempt fees or delayed routes.
Why Clear Service Requirements Matter
The simpler your shipping instructions, the fewer hold-ups. Full transparency about site limitations (e.g., limited access, residential areas, narrow receiving windows) helps carriers plan effectively. This often means your freight moves along with minimal friction.
Final-Mile Delivery Considerations
Residential vs. Commercial Speed Differences
Dropping at a residential address often involves narrower roads, limited access, or time-of-day restrictions. This can push the driver to make extra calls or attempts, prolonging the shipment’s final leg. Proactively informing carriers about special unloading conditions ensures the correct equipment and scheduling from the outset.
Collaboration with Last-Mile Providers
For e-commerce or direct-to-consumer shipments, last-mile specialists or parcel carriers might handle the final segment. Close coordination between the LTL carrier and last-mile provider can reduce transit overlap or missed connections—ultimately speeding up doorstep delivery.
Building Strong Carrier Relationships
Volume Commitments and Rate Agreements
Carriers value consistent shippers. By pledging a steady flow of shipments or negotiating annual contracts, you can request:
- Priority Loading: Carriers might allocate capacity for regular customers first.
- Faster Transits: Some carriers tailor expedited LTL lanes for high-volume accounts.
How Trust Reduces Administrative Bottlenecks
When carriers trust your shipping data—like correct weights, packaging, and limited or no claims—they expedite administrative tasks. Less verification means your freight can skip certain processes or inspections at cross-dock facilities, trimming precious hours or days off transit.
Conclusion
Achieving faster LTL freight delivery times need not be daunting. By focusing on accurate shipment data, well-chosen carriers, consistent communication, and leveraging tools like TMS or consolidation techniques, you can streamline cross-dock transfers and reduce the risk of missed cutoffs. Preparation is paramount—thorough packaging, honest classification, and anticipating seasonal peaks help ensure your partial loads arrive on schedule.
While LTL inherently involves more stops than full-truck shipments, proactive planning can bridge the speed gap, giving you the best of both worlds: cost-effectiveness and timely delivery. As your business and shipping volumes evolve, continuous improvement in these areas will keep your LTL operations efficient and competitive.
How useful was this post?
Click on a star to rate it!
Average rating 0 / 5. Vote count: 0
No votes so far! Be the first to rate this post.